Core Advantages
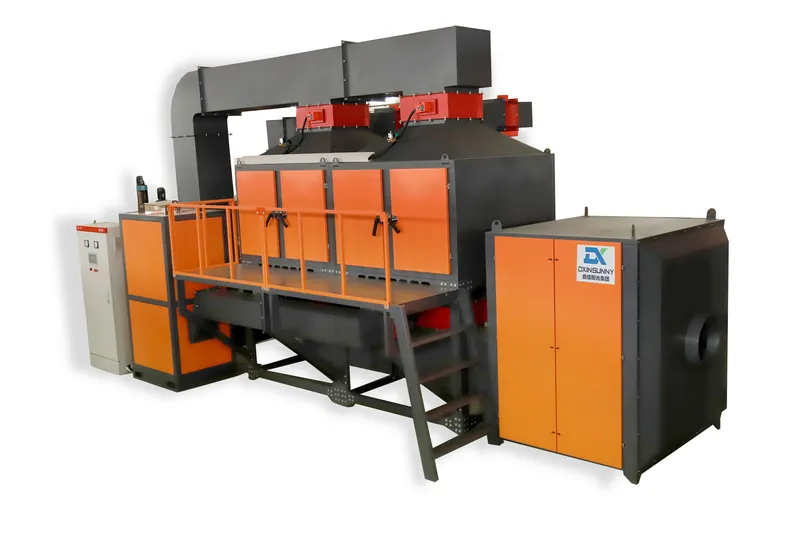
Effective Pollutant Destruction:
- Combustion type equipment efficiently destroys harmful pollutants in waste gases, including volatile organic compounds (VOCs), hazardous air pollutants (HAPs), and odors, through high-temperature combustion processes. This results in significant reductions of harmful emissions and ensures compliance with environmental regulations.
Energy Recovery Potential:
- Many combustion systems are designed to recover energy from the combustion process, which can be harnessed for heating or electricity generation. This not only improves overall system efficiency but also reduces operational costs by utilizing waste energy that would otherwise be lost.
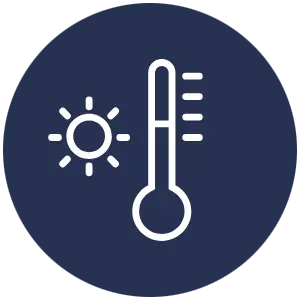
High Destruction Efficiency
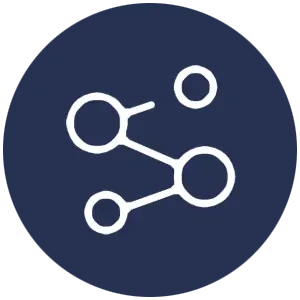
Versatility
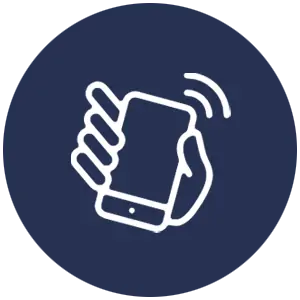
Energy Recovery
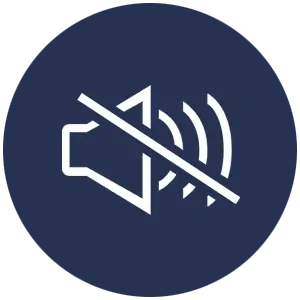
Compliance with Regulations
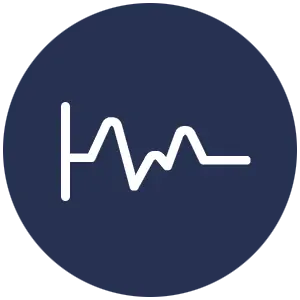
Reduced Odor Emissions
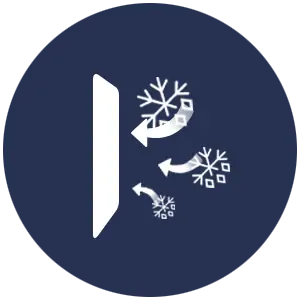
Minimal Residual Waste
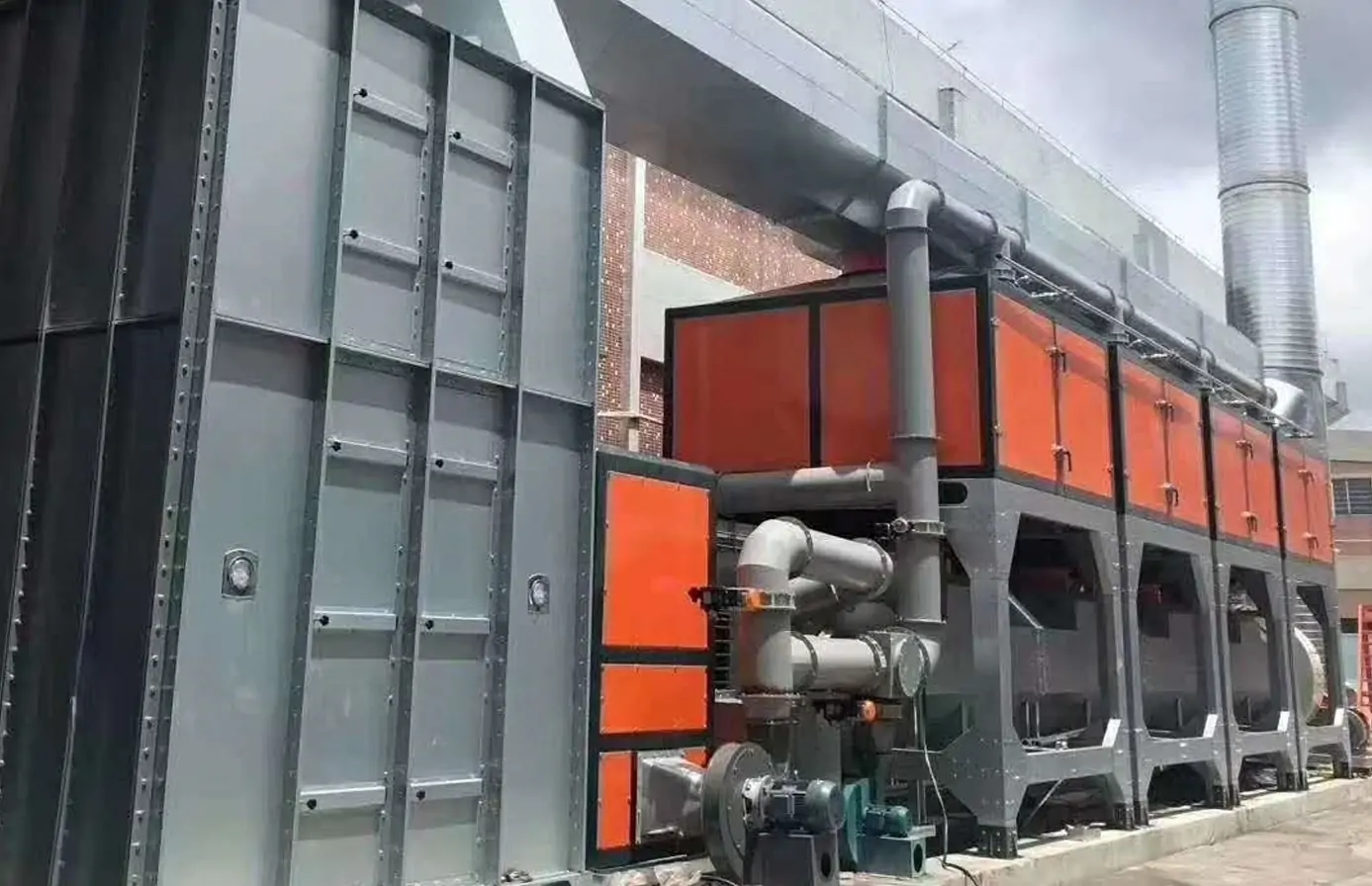
High Destruction Efficiency:
- Combustion type systems are capable of achieving destruction efficiencies often exceeding 98%. They operate at high temperatures, typically between 800°C and 1,200°C (1,472°F to 2,192°F), allowing for the complete oxidation of organic compounds. This high level of efficiency ensures that the majority of harmful pollutants are converted into less harmful substances, such as carbon dioxide (CO₂) and water vapor, significantly reducing the environmental impact of waste gases.
Versatility:
- Combustion systems are designed to handle a wide range of waste gases produced across various industries, including chemical manufacturing, oil refining, food processing, and pharmaceuticals. They can effectively treat different types of gases, such as VOCs, HAPs, and other odorous compounds, making them adaptable to specific operational needs and pollutant profiles.
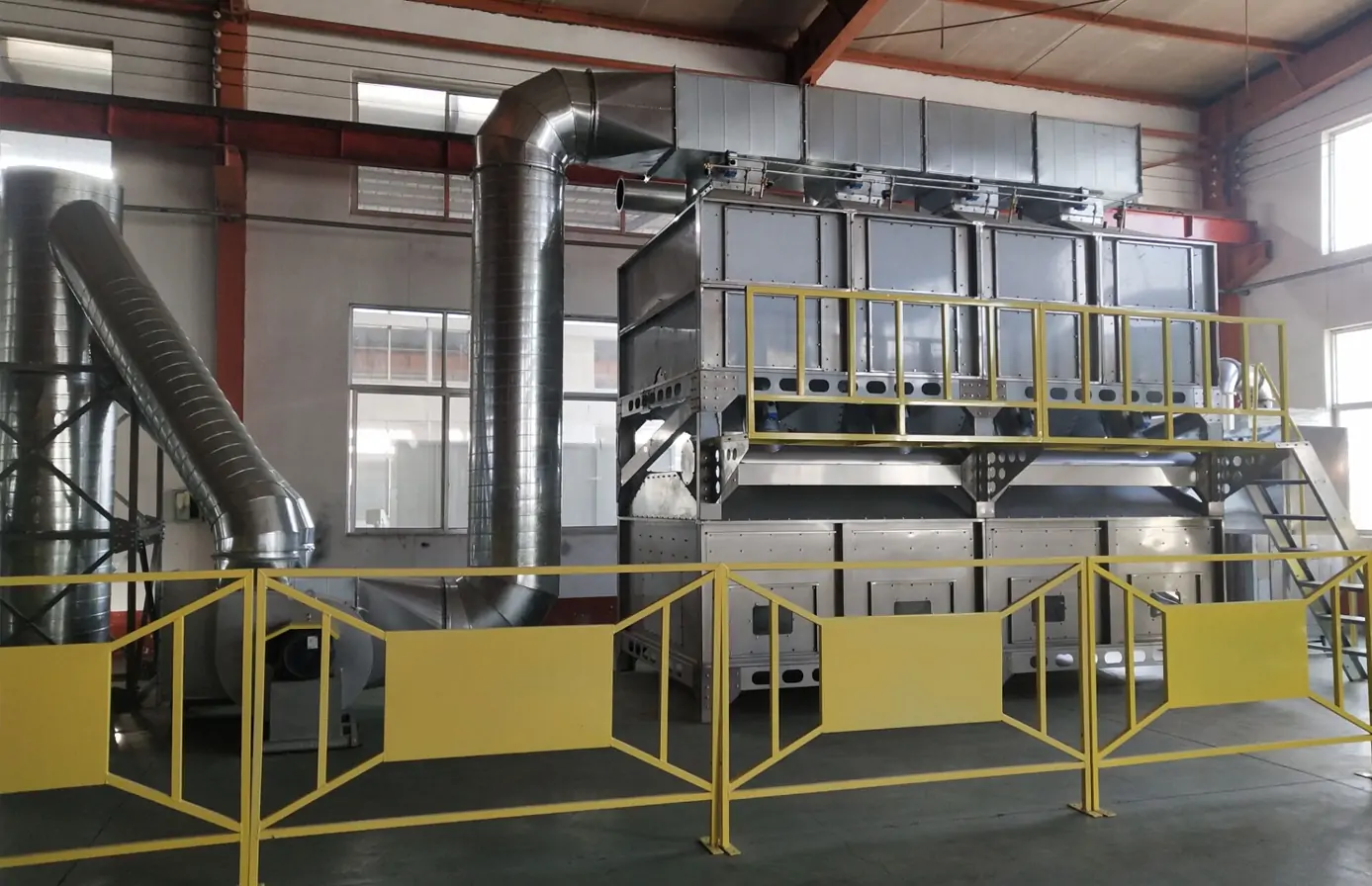
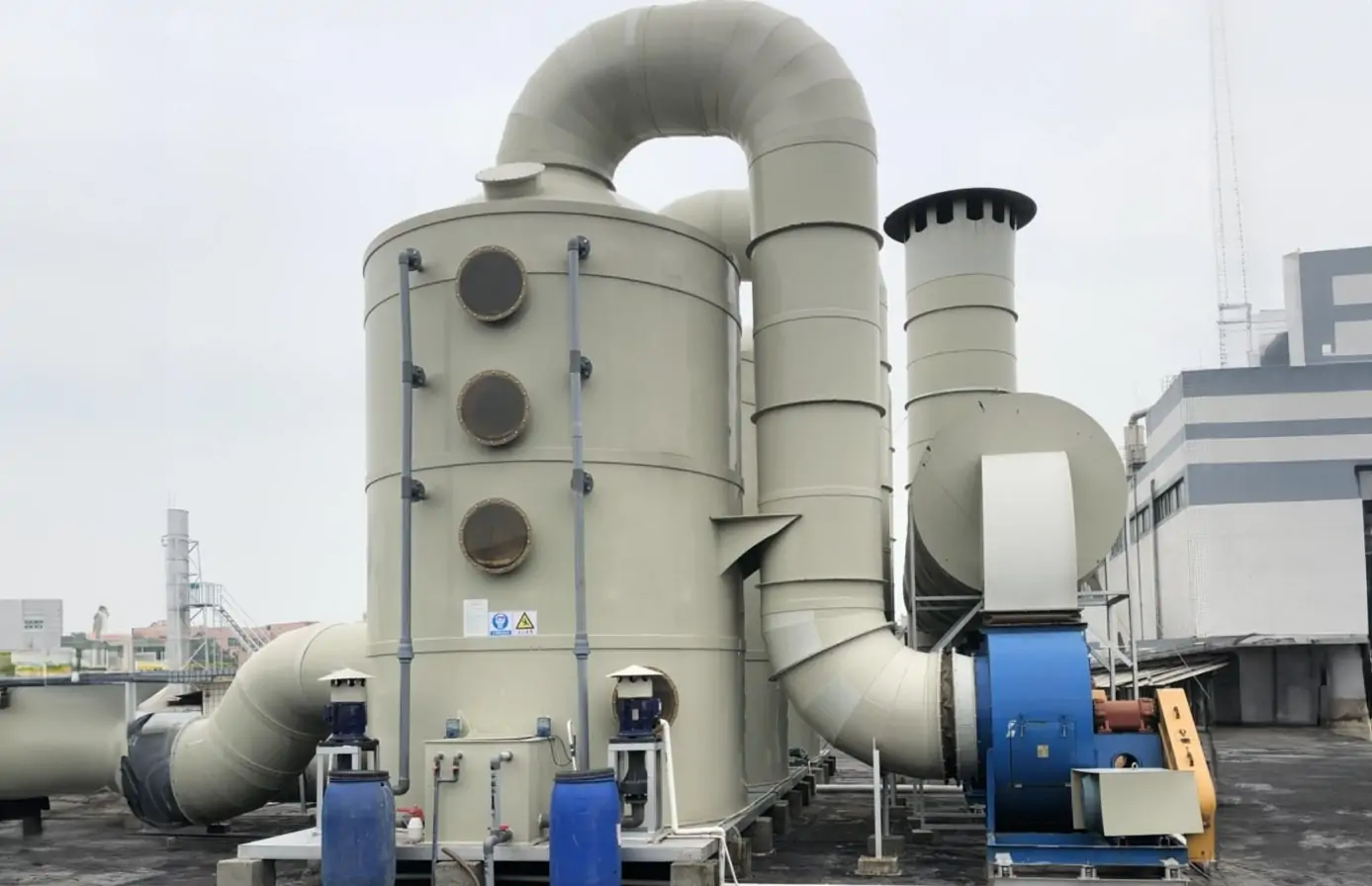
Energy Recovery:
- Many modern combustion systems are equipped with energy recovery features, such as heat exchangers, that capture waste heat generated during combustion. This recovered energy can be used to preheat incoming air or process fluids, or even generate electricity, thereby increasing the overall efficiency of the system. By recovering and utilizing this energy, facilities can significantly lower their operational costs and carbon footprint.
Compliance with Regulations:
- Combustion type waste gas treatment equipment plays a crucial role in helping industries meet stringent environmental regulations imposed by government bodies. Effective pollutant destruction minimizes the risk of non-compliance with air quality standards, thereby avoiding potential fines and legal issues. Furthermore, by implementing such technologies, companies enhance their sustainability credentials, contributing positively to their corporate image.
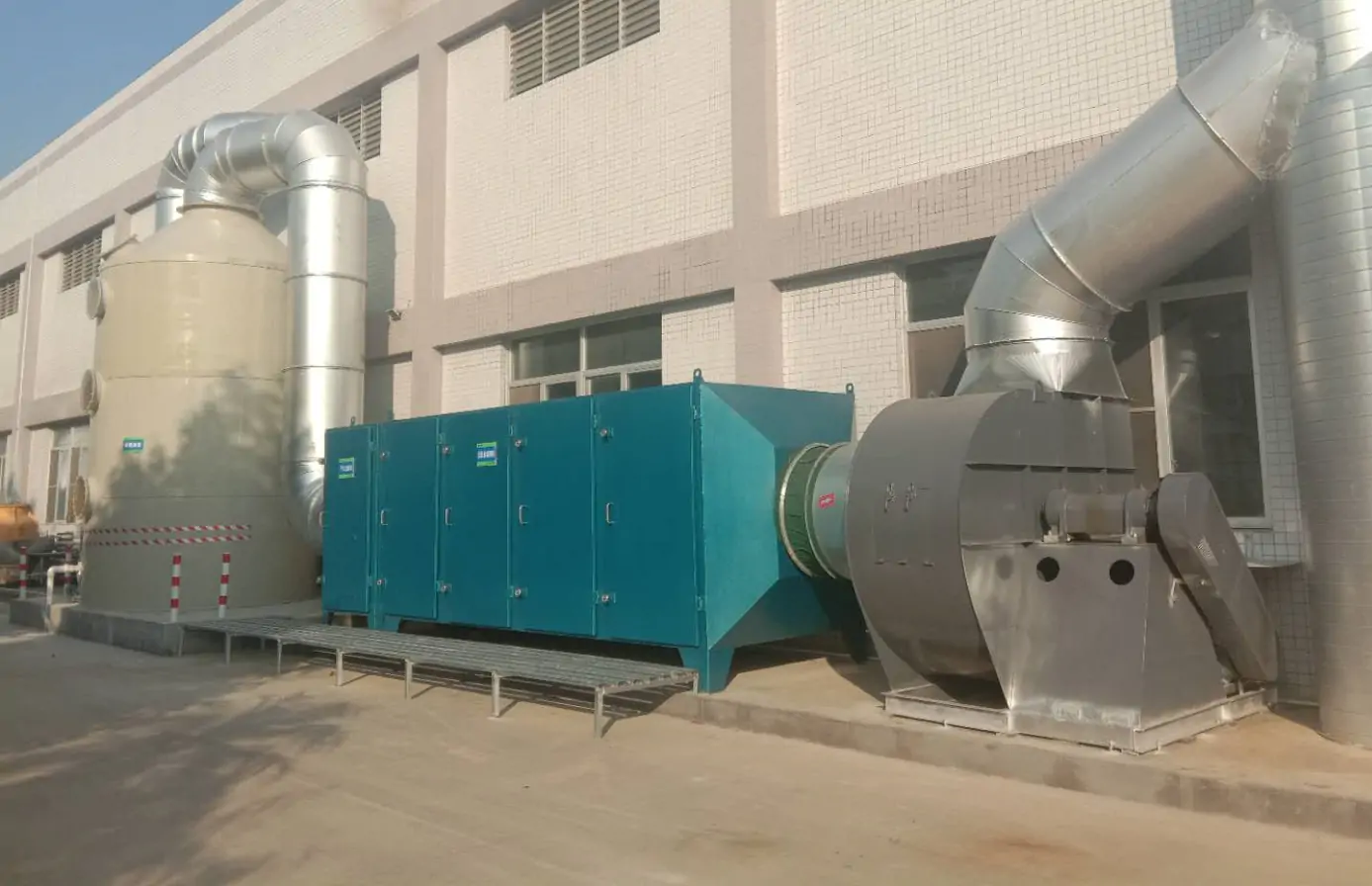
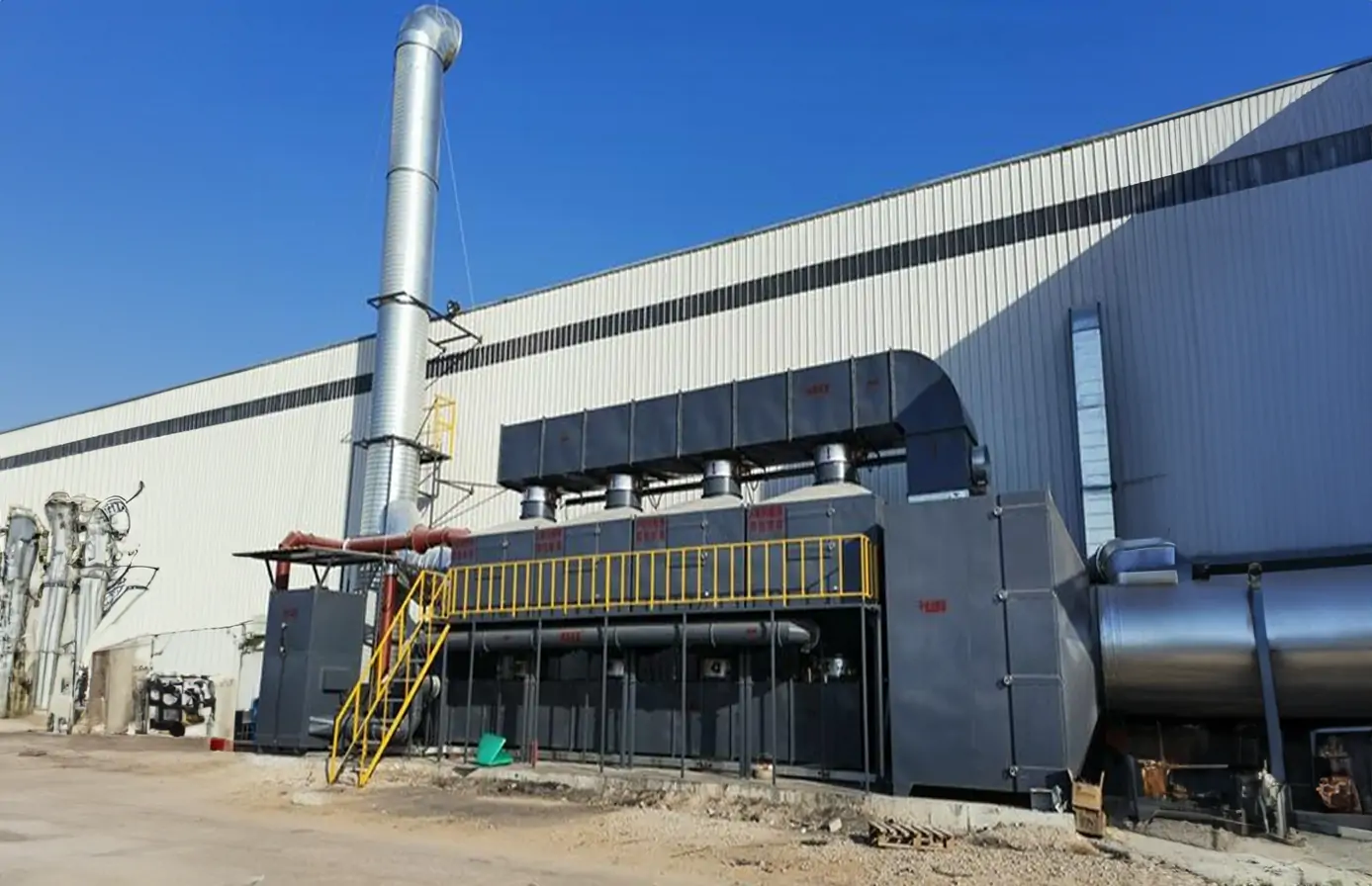
Reduced Odor Emissions:
- Odorous compounds, such as those produced during chemical manufacturing or waste treatment processes, can create significant issues for both workers and surrounding communities. Combustion systems effectively break down these compounds during the combustion process, reducing or eliminating unpleasant odors. This improvement in air quality contributes to a healthier work environment and a better relationship with neighboring communities.
Minimal Residual Waste:
- Unlike some other waste gas treatment technologies, which may produce significant solid or liquid residuals that require disposal, combustion systems convert most of the organic pollutants into gaseous byproducts (CO₂ and water vapor). This conversion minimizes the generation of residual waste, simplifying the waste management process and reducing the environmental impact associated with disposal.
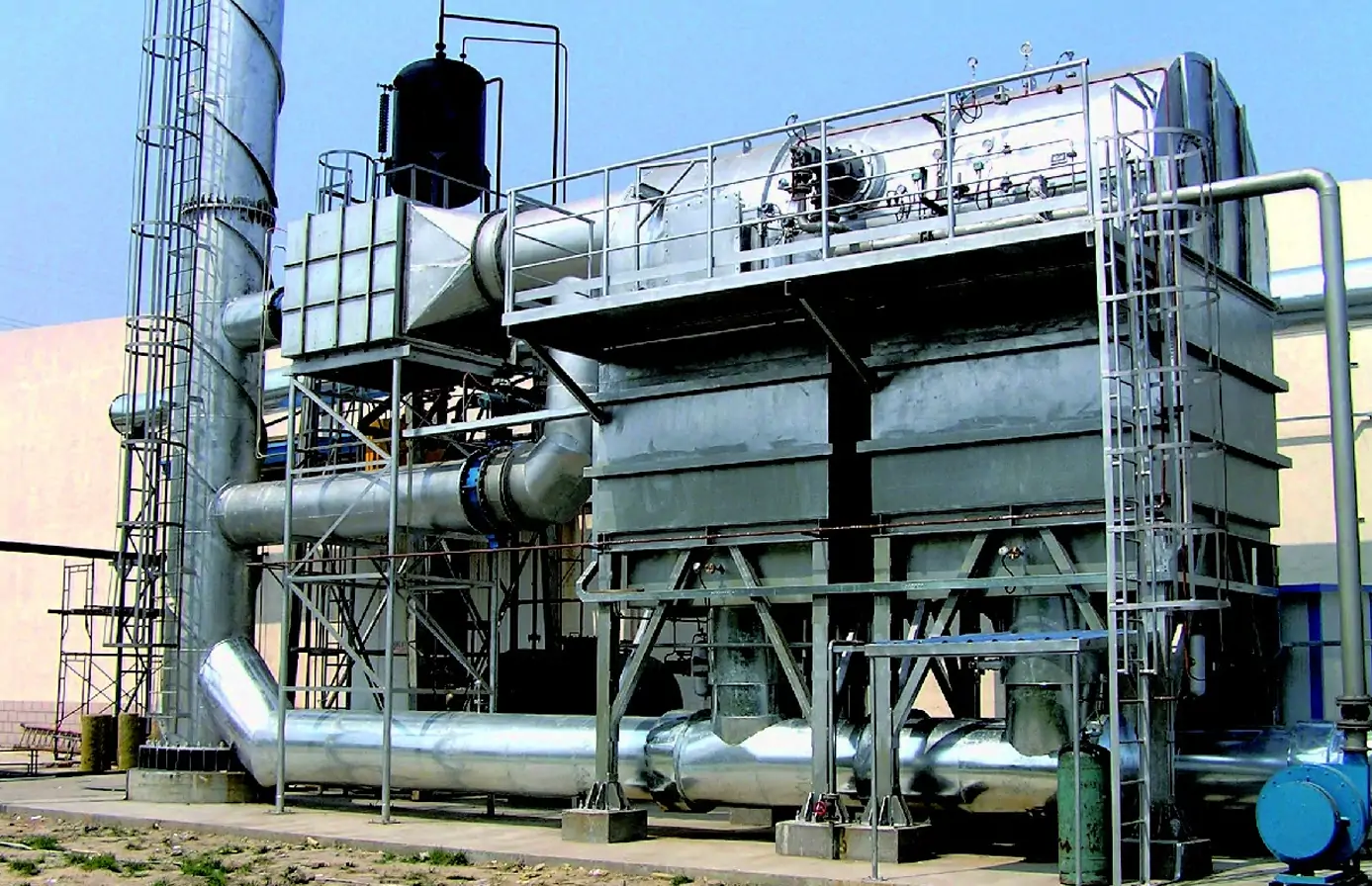
Product Specifications
Product Specification | Details | Product Specification | Details |
Heating Power | 6.0 kW | Energy Efficiency Rating | A++ |
Refrigerant Type | R410A | Applicable Area | 50-150㎡ |
Power Supply Voltage | 220V / 50Hz | Noise Level | ≤25 dB |
Dual Inverter Technology | Supported | Smart Temperature Control | Supported |
Remote Control | Mobile App Remote Control | Auto Defrost Function | Supported |
Operating Temp Range | -15℃ to 45℃ | Weight | 40 kg |
Dimensions (L x W x H) | 850mm x 300mm x 650mm | Installation Method | Ceiling / Wall Mounted |
combustion type waste gas treatment equipment Feature and Application:
Application:
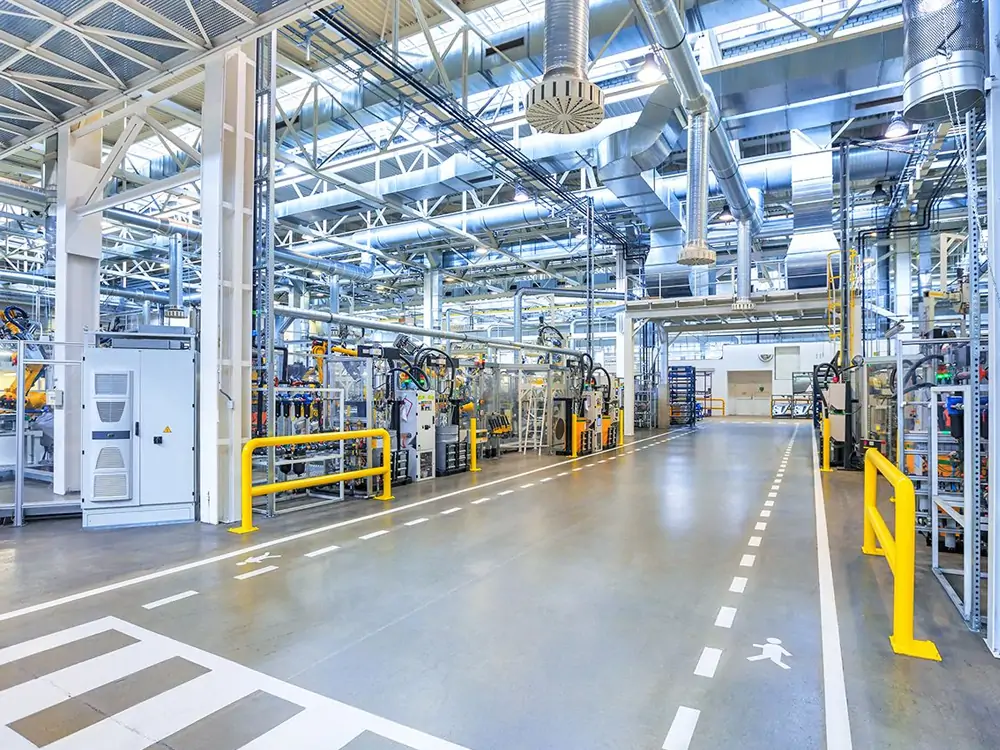
Chemical Manufacturing:
Combustion systems are used to treat volatile organic compounds (VOCs) and other hazardous air pollutants (HAPs) generated during the production of chemicals, ensuring compliance with environmental regulations and reducing emissions.
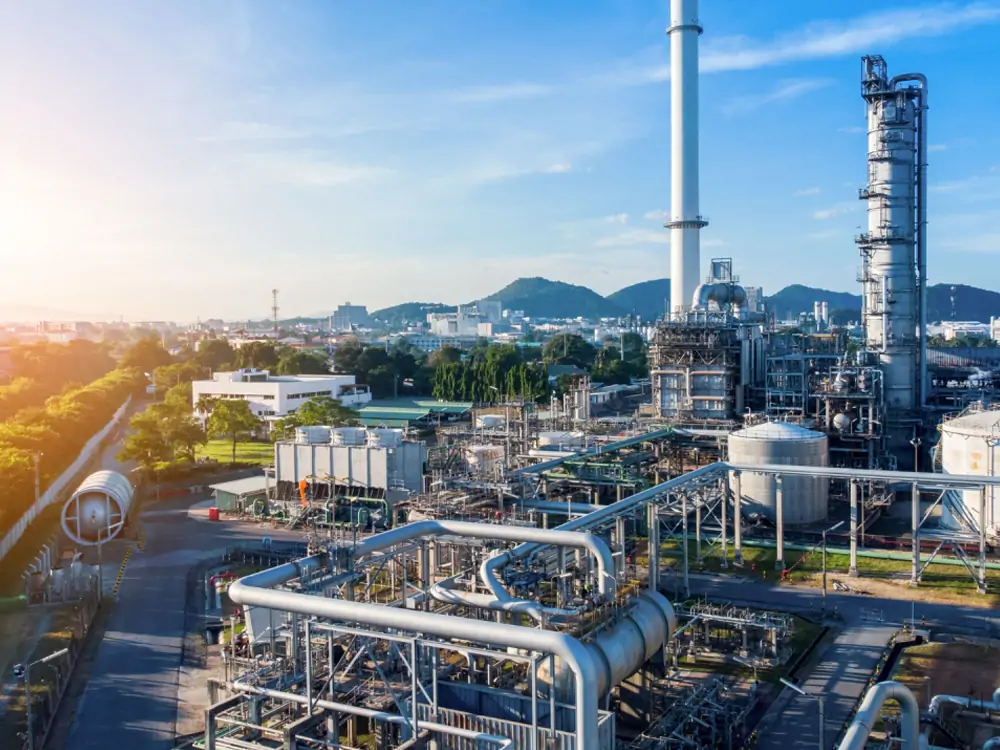
Oil Refining:
In oil refineries, combustion type equipment effectively manages waste gases containing sulfur compounds, VOCs, and other pollutants produced during refining processes, minimizing environmental impact and odor issues.
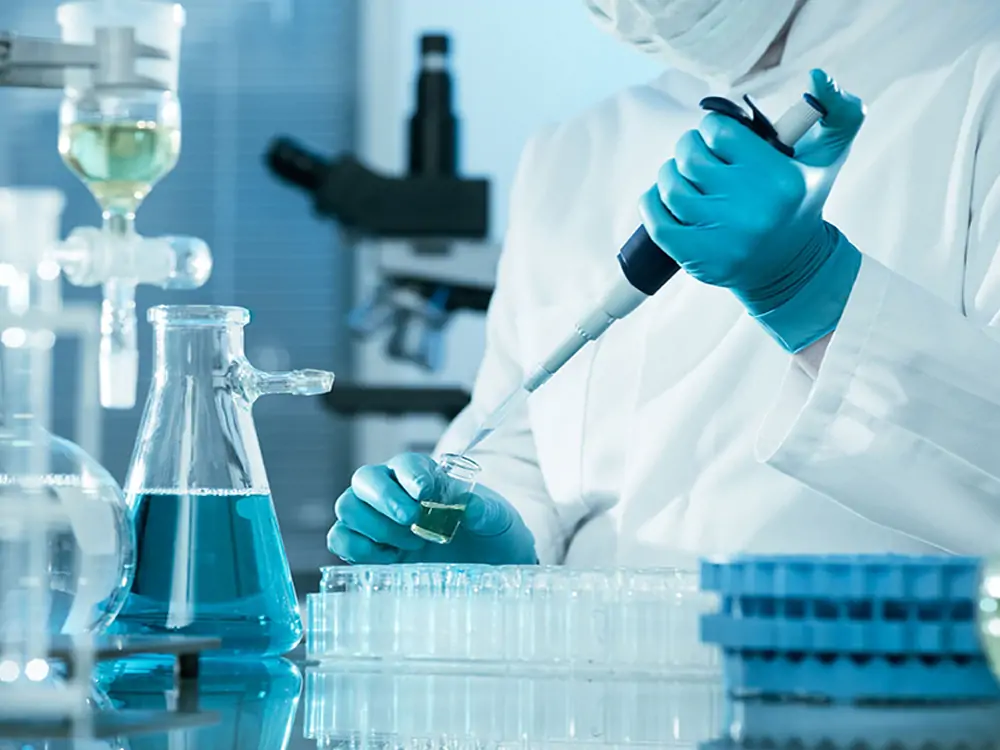
Pharmaceutical Production:
The pharmaceutical industry uses combustion systems to treat exhaust gases containing solvents and byproducts from drug manufacturing, ensuring high destruction efficiencies for hazardous emissions and meeting regulatory requirements.
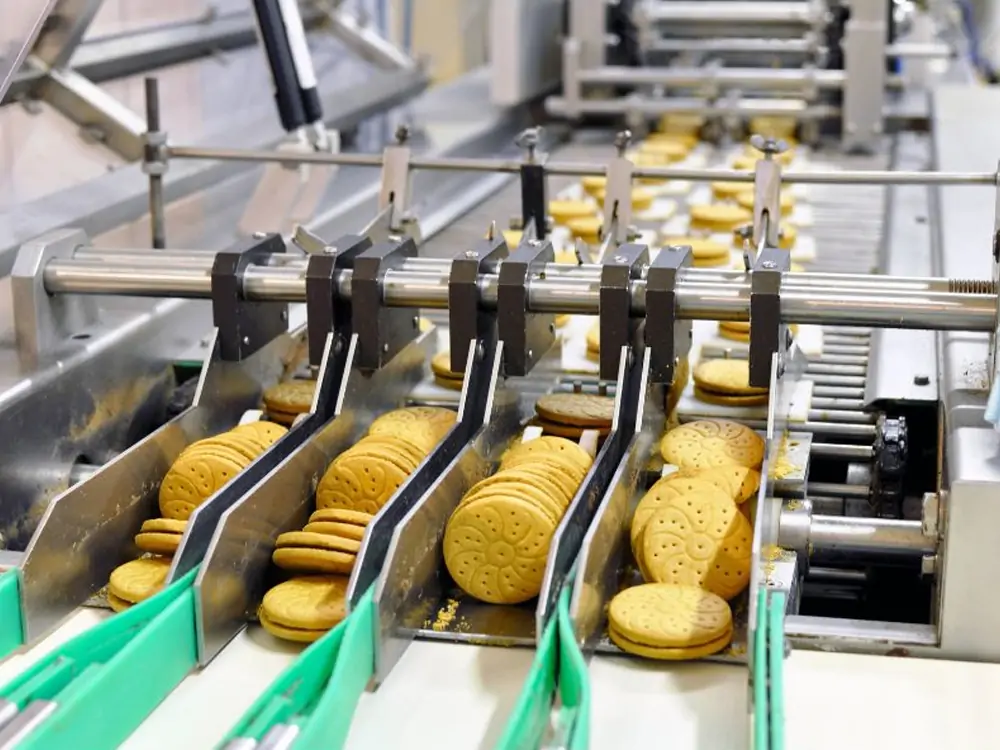
Food Processing:
Combustion systems help control and eliminate odors and emissions generated during food processing operations, such as frying or cooking, contributing to improved air quality for both workers and nearby communities.
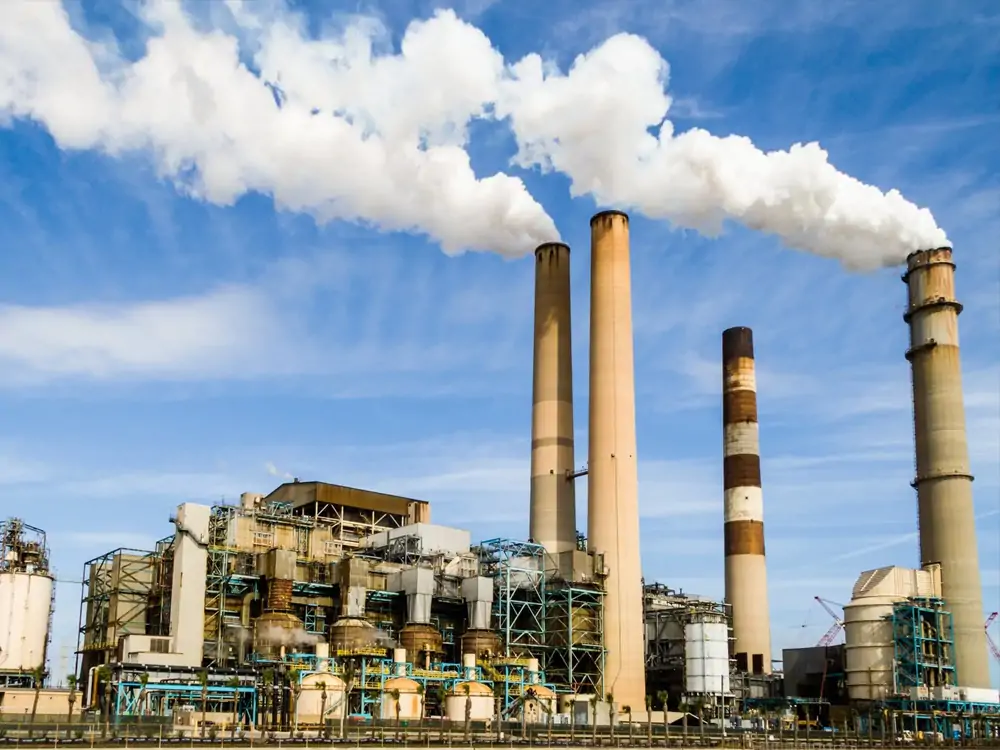
Waste Incineration:
Combustion technology is employed in waste-to-energy plants to incinerate municipal and industrial waste, converting it into energy while minimizing the release of harmful emissions through effective pollutant destruction.
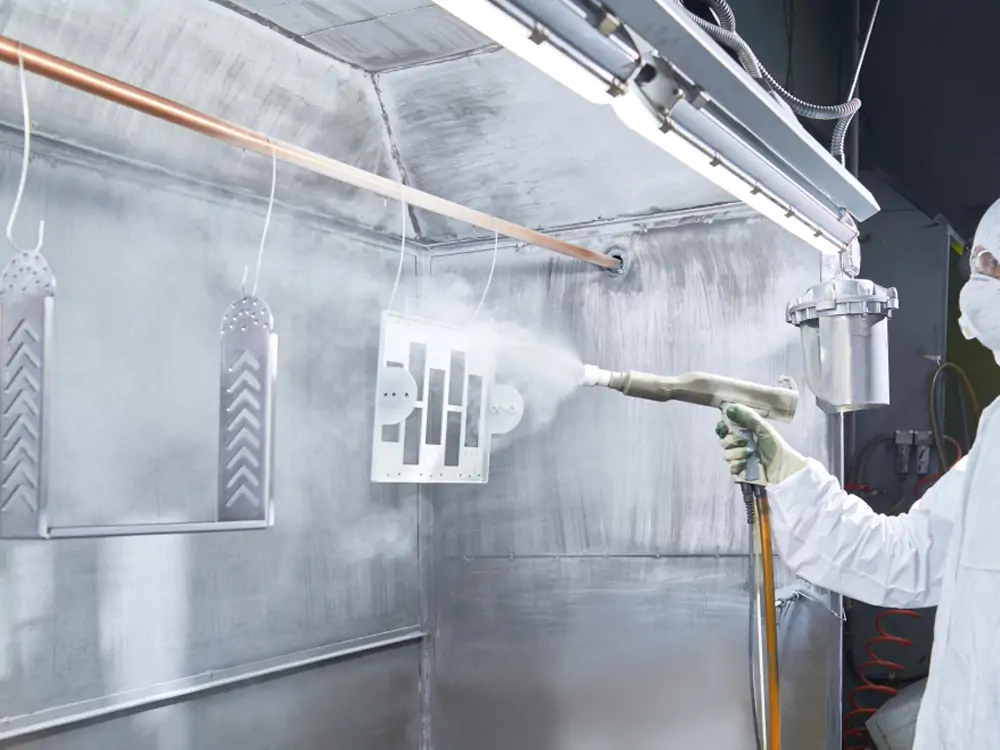
Paint and Coating Industries:
In industries that use spray painting or coating processes, combustion type waste gas treatment equipment manages VOCs and solvents released during application, ensuring cleaner air and compliance with strict environmental standards.
combustion type waste gas treatment equipment Details
Working Principle:
Gas Inlet and Pre-treatment:
Contaminated waste gases are first drawn into the combustion system through an inlet. In some cases, pre-treatment steps such as cooling or filtration may be employed to remove larger particles or reduce the temperature of the incoming gases, ensuring that they are at optimal conditions for combustion.
Combustion Chamber:
The treated gases enter a combustion chamber where they are mixed with a fuel source (such as natural gas, propane, or even the organic solvents present in the waste gas) and ignited. This combustion process occurs at high temperatures, typically between 800°C and 1,200°C (1,472°F and 2,192°F). The high temperature provides the energy necessary to oxidize the pollutants, breaking them down into simpler and less harmful substances
Heat Recovery and Emission Control:
Many combustion systems are equipped with heat recovery units that capture excess heat generated during combustion. This recovered energy can be reused to preheat incoming gases or for other industrial processes, enhancing overall energy efficiency. After combustion, the exhaust gases may pass through additional emission control devices, such as scrubbers or filters, to further reduce any residual pollutants or particulates before being released into the atmosphere.
Clean Air Discharge:
Finally, the treated and purified gases are discharged into the atmosphere through a stack or exhaust outlet. The system ensures that emissions comply with local and federal environmental regulations, contributing to improved air quality and minimizing environmental impact
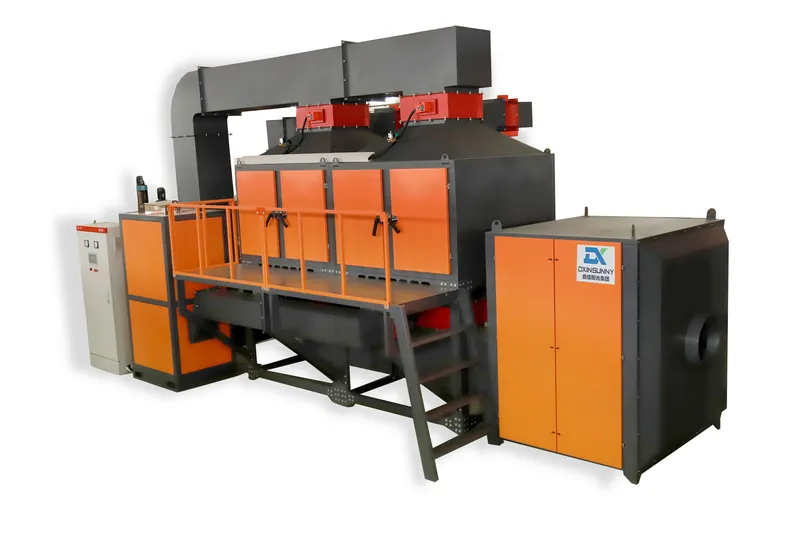
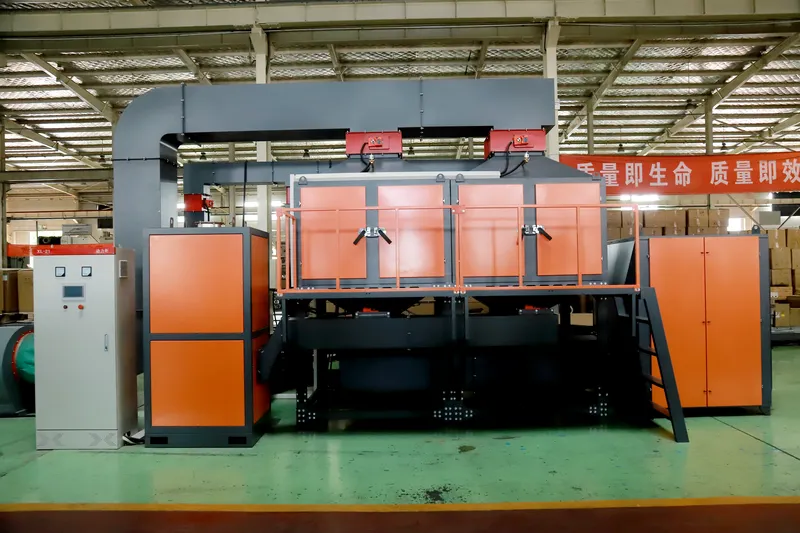
Efficiency and Performance:
Efficiency and Performance of combustion type waste gas treatment equipment are defined by the system’s ability to effectively destroy pollutants while maintaining optimal operational costs. These systems typically achieve destruction efficiencies of over 98% for a wide range of pollutants, including volatile organic compounds (VOCs), hazardous air pollutants (HAPs), and odorous compounds, by operating at high temperatures between 800°C and 1,200°C (1,472°F to 2,192°F).
Energy recovery systems, such as heat exchangers, enhance overall performance by capturing excess heat generated during the combustion process, allowing for reuse in other industrial processes or preheating incoming gases. This integration of energy recovery can significantly lower operational costs and improve the system’s energy efficiency.
In terms of reliability, advanced combustion control and monitoring systems ensure that the equipment maintains consistent performance even under varying waste gas flow rates or pollutant concentrations. This combination of high destruction efficiency, energy recovery, and real-time monitoring allows combustion type waste gas treatment systems to deliver both cost-effective and environmentally compliant solutions across various industries.
Frequently asked questions
Combustion systems are highly effective in treating volatile organic compounds (VOCs), hazardous air pollutants (HAPs), sulfur compounds, odors, and other organic contaminants. They convert these pollutants into harmless byproducts like carbon dioxide and water vapor through high-temperature oxidation.
Industries such as chemical manufacturing, oil refining, pharmaceuticals, food processing, waste incineration, and paint/coating industries use these systems to treat their waste gases and comply with environmental regulations.
Many combustion systems are equipped with energy recovery features, such as heat exchangers, that capture waste heat from the combustion process. This recovered energy can be reused in industrial processes, improving overall energy efficiency and reducing operational costs.
Regular maintenance includes inspecting the combustion chamber, cleaning or replacing nozzles, monitoring burner efficiency, checking for leaks, and ensuring proper operation of heat recovery units. Proper maintenance helps maintain efficiency and ensures reliable long-term operation.
Combustion systems typically achieve pollutant destruction efficiencies above 98%, effectively reducing harmful emissions to meet or exceed environmental regulatory standards. This includes minimizing emissions of VOCs, odors, and other harmful air pollutants.
Yes, combustion systems can be customized based on the specific type and volume of waste gases produced by a facility. Customization options include adjusting the size of the combustion chamber, integrating heat recovery systems, and tailoring emission control features to meet specific regulatory and operational requirements.