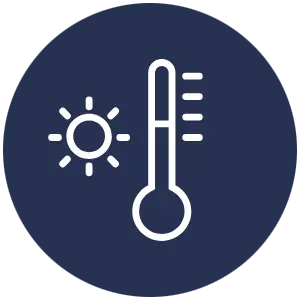
Advanced Separation
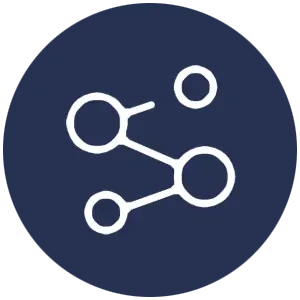
Accurate Level Control
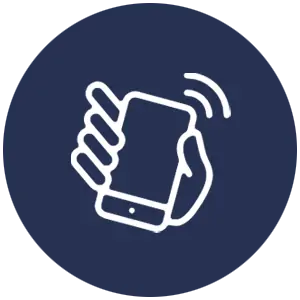
Corrosion Protection
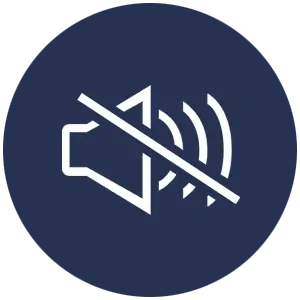
Efficient Pumping
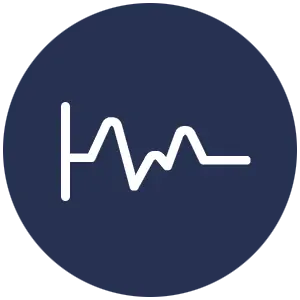
Automation Integration
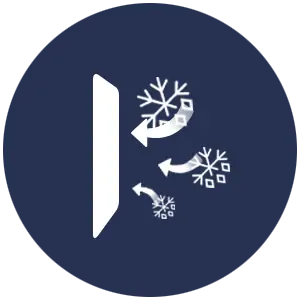
Modular Design
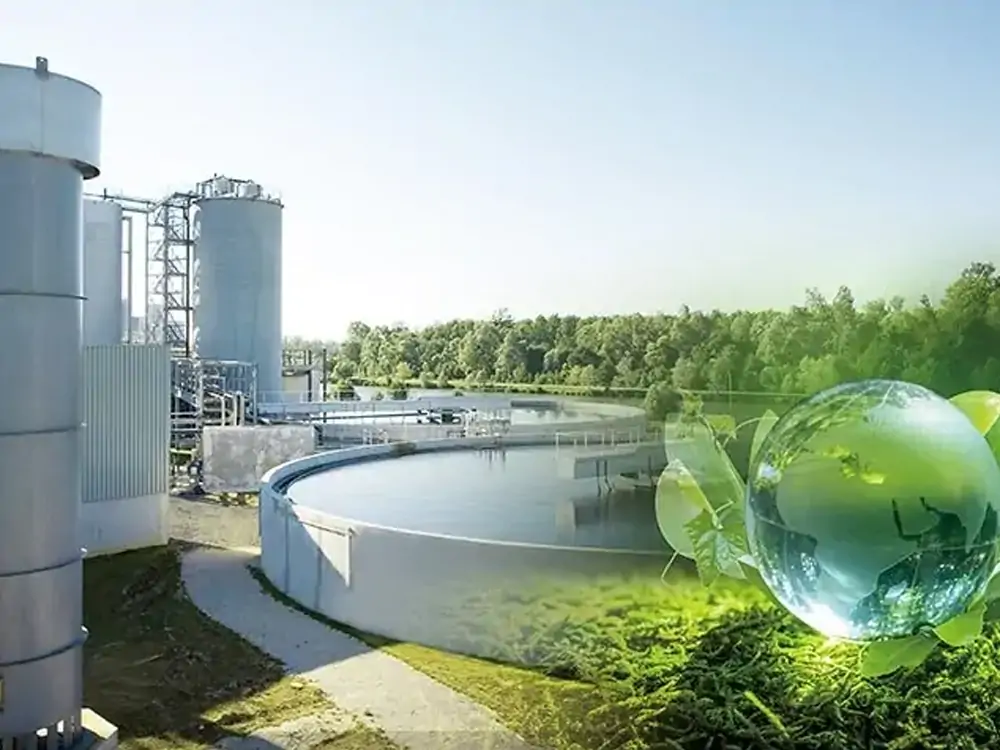
Advanced Separation
Accurate Level Control
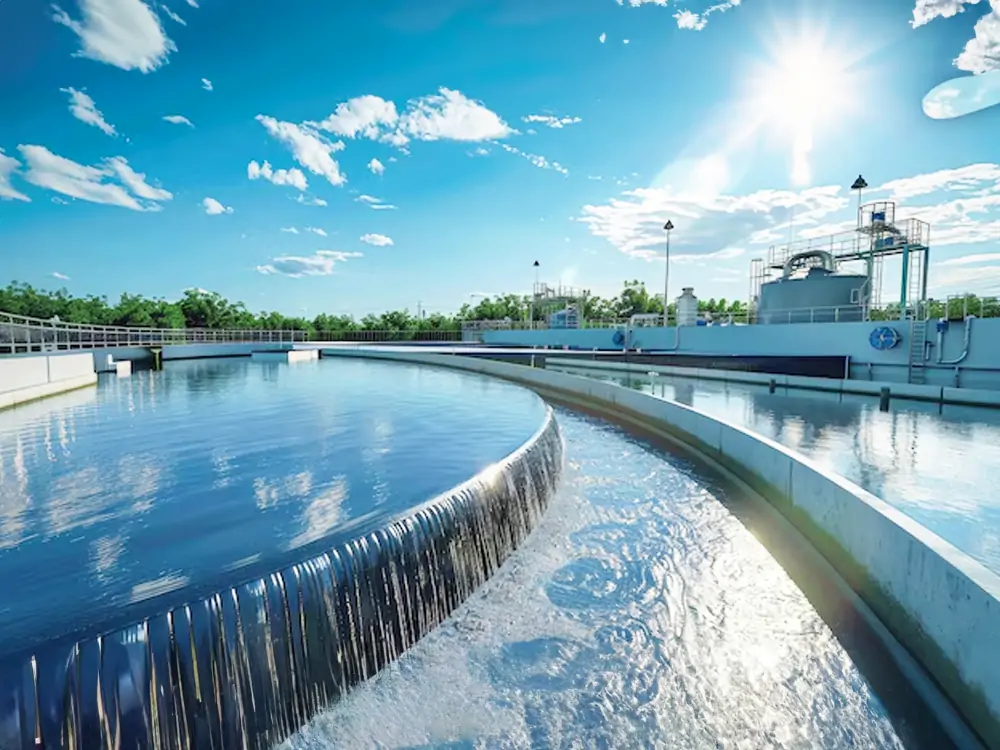
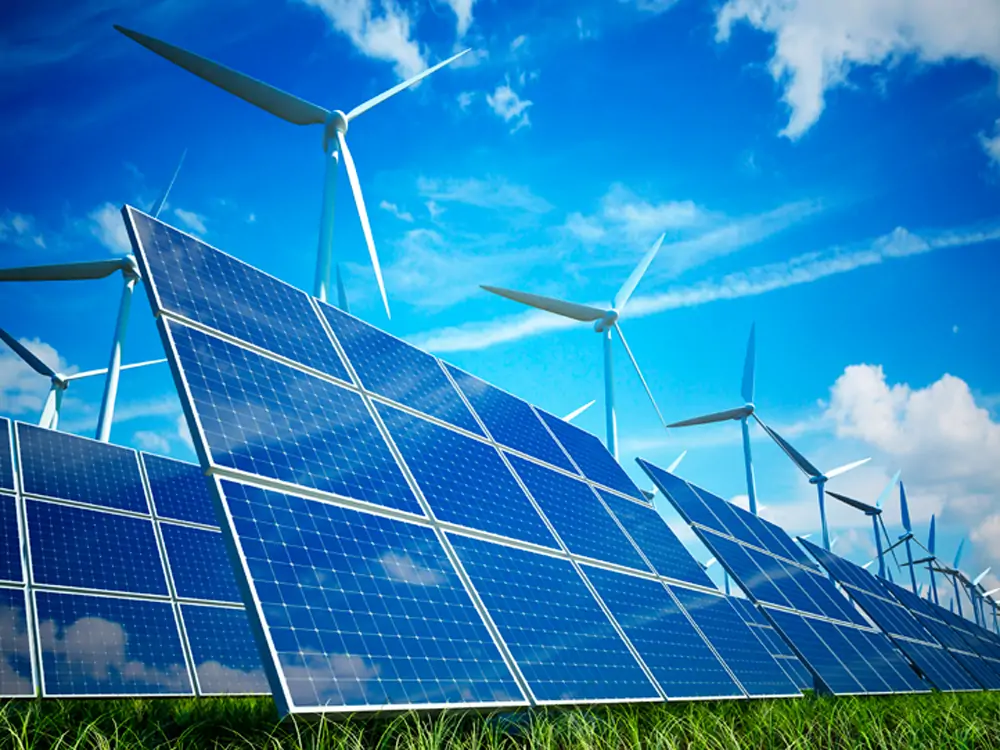
Corrosion Protection
Efficient Pumping
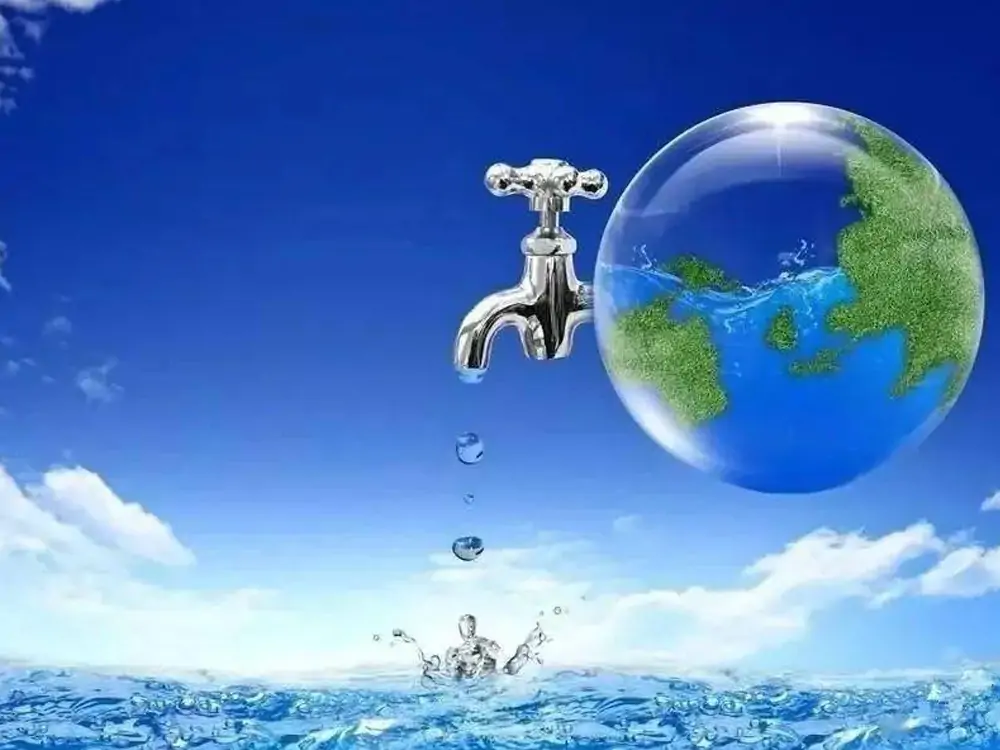
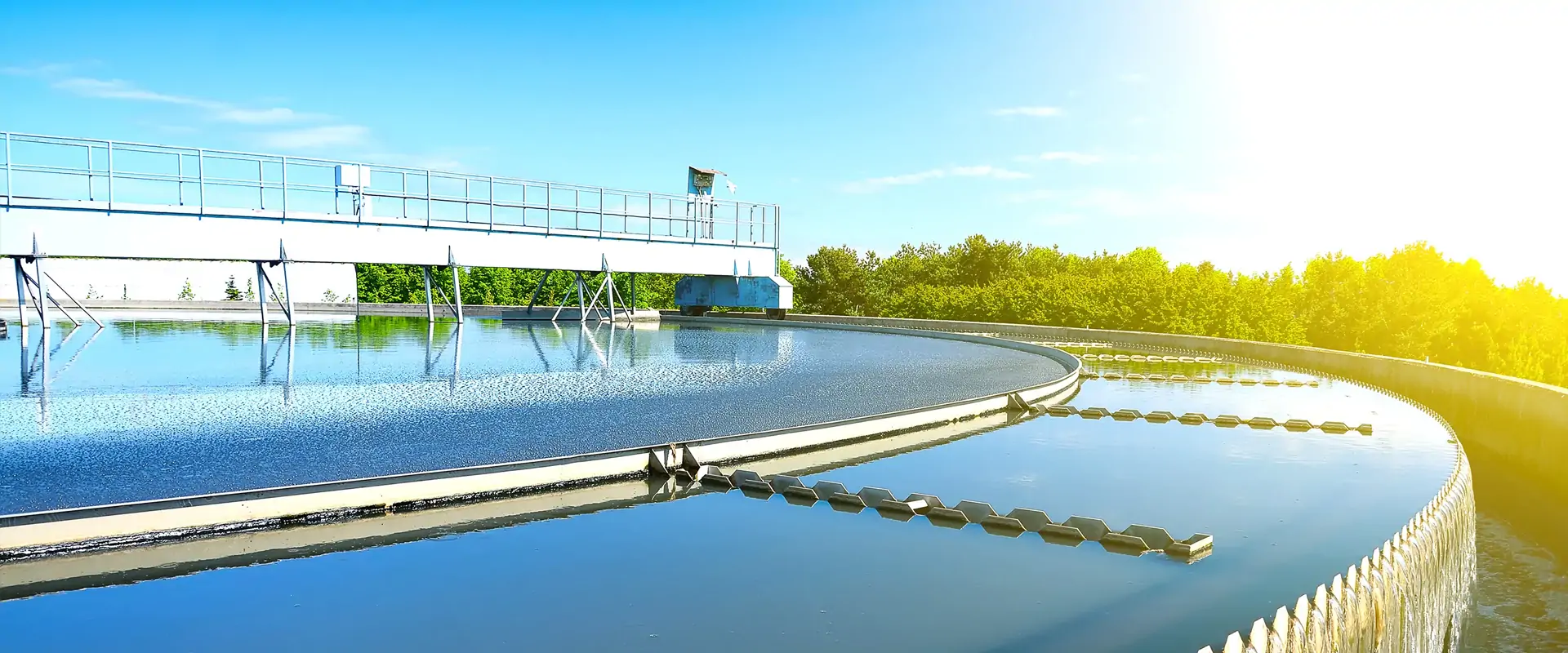
Automation Integration
Modular Design
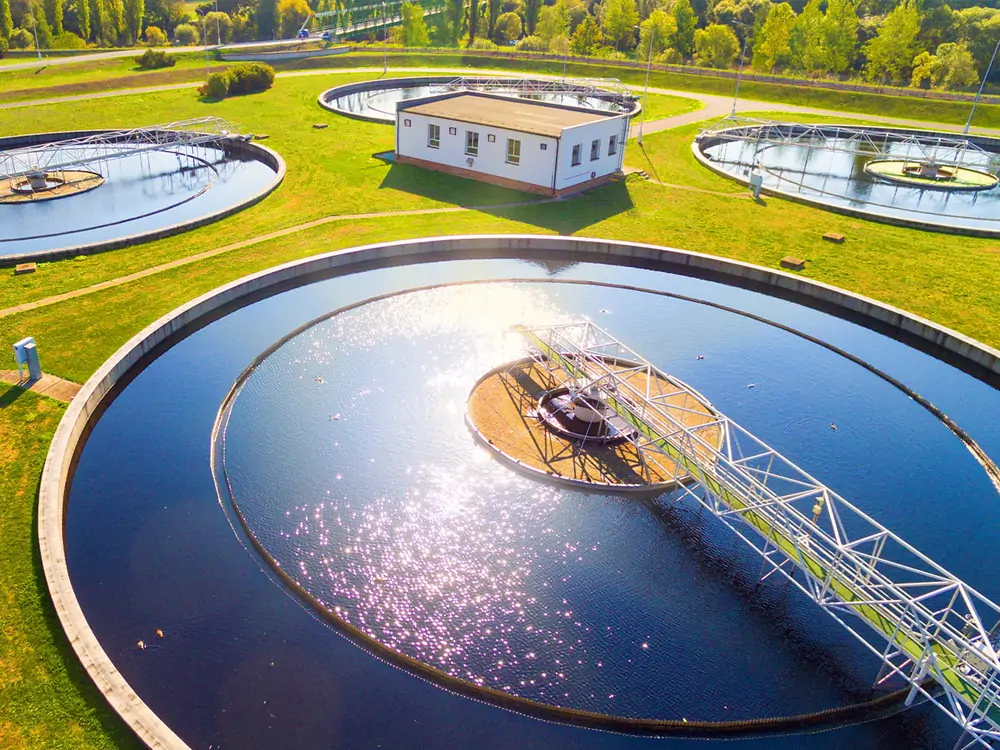
Product Specifications
Product Specification | Details | Product Specification | Details |
Heating Power | 6.0 kW | Energy Efficiency Rating | A++ |
Refrigerant Type | R410A | Applicable Area | 50-150㎡ |
Power Supply Voltage | 220V / 50Hz | Noise Level | ≤25 dB |
Dual Inverter Technology | Supported | Smart Temperature Control | Supported |
Remote Control | Mobile App Remote Control | Auto Defrost Function | Supported |
Operating Temp Range | -15℃ to 45℃ | Weight | 40 kg |
Dimensions (L x W x H) | 850mm x 300mm x 650mm | Installation Method | Ceiling / Wall Mounted |
condensate recovery equipment Feature and Application:
Application:
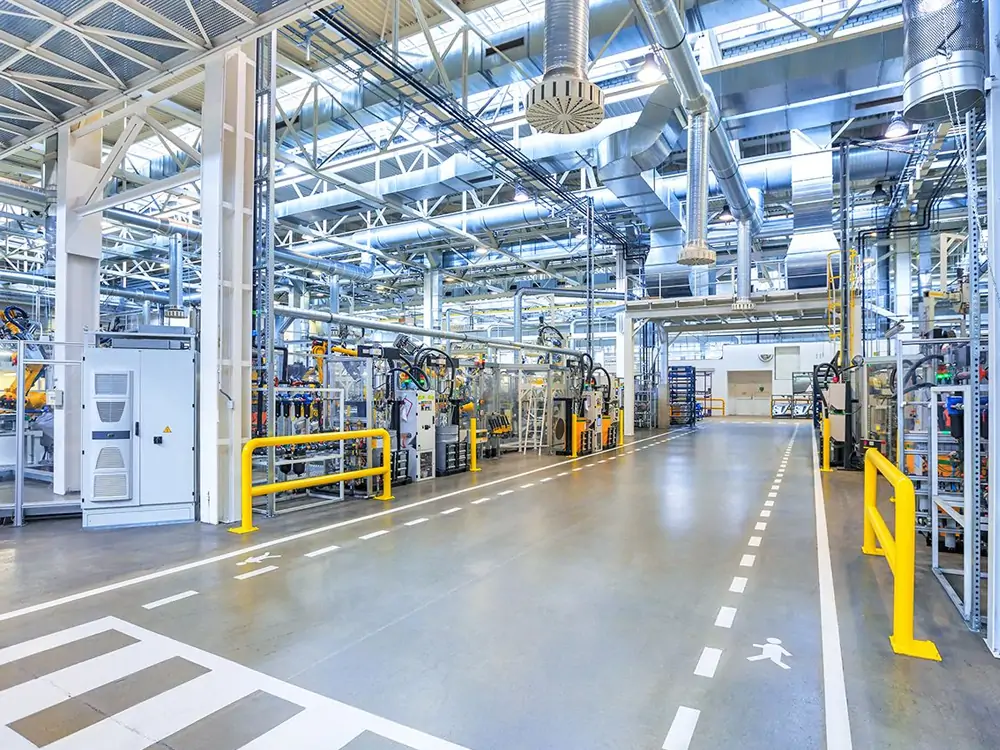
Industrial Boilers
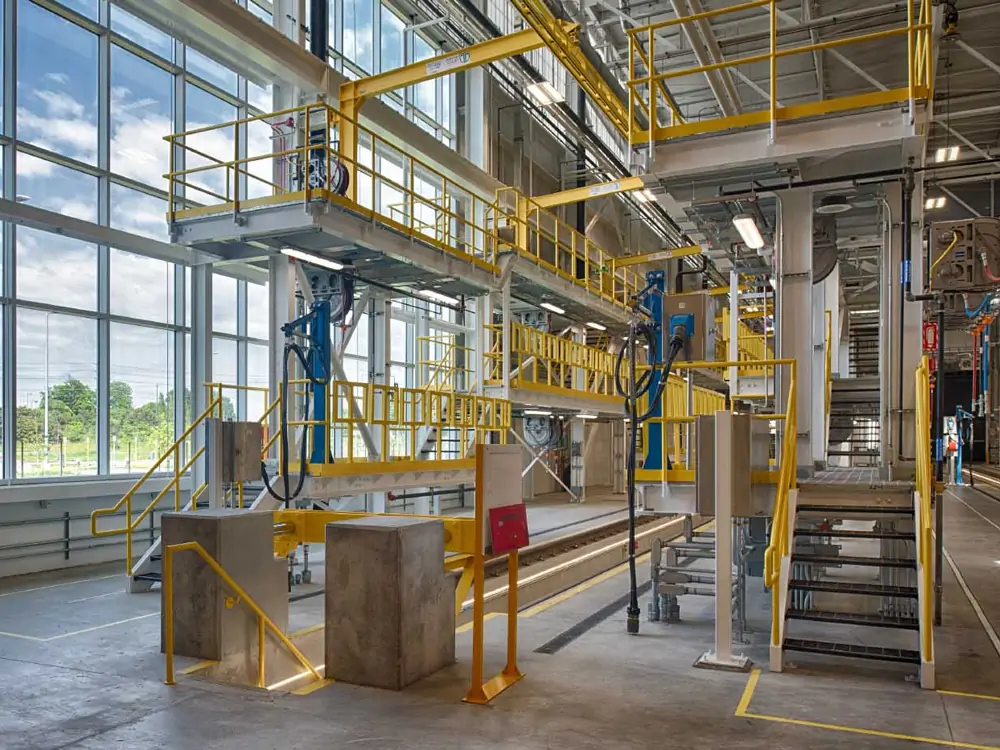
HVAC (Heating, Ventilation, and Air – Conditioning) Systems
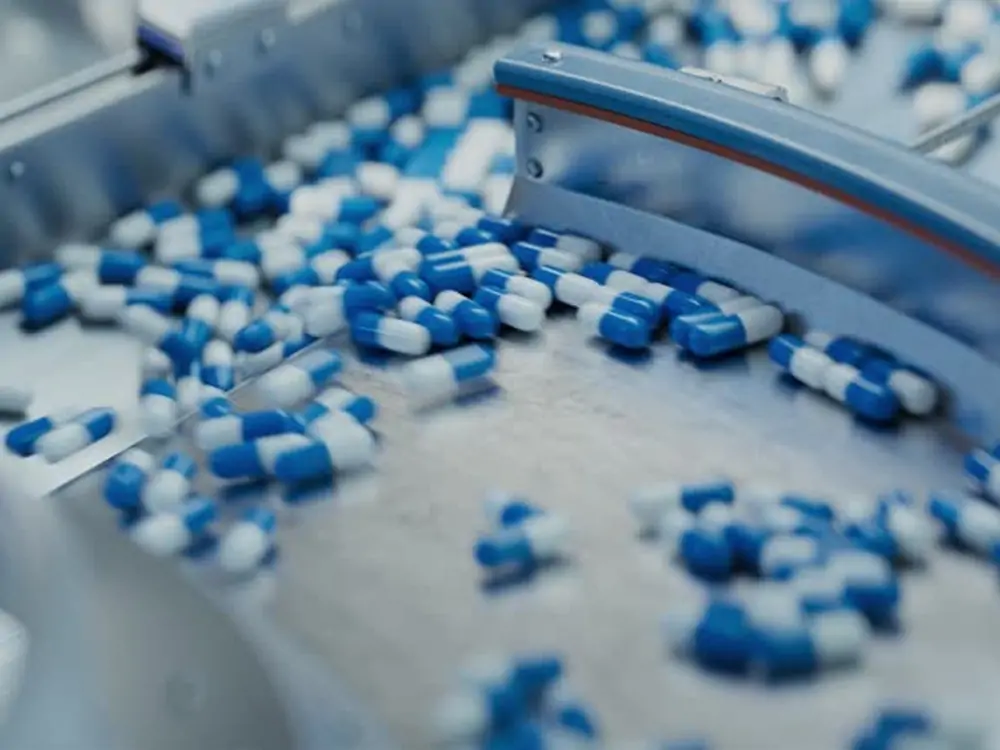
Chemical and Petrochemical Plants
Chemical and petrochemical plants have numerous processes that involve the use of steam for heating, reaction, or distillation. The condensate recovery equipment in these plants is crucial for recovering valuable chemicals that may be dissolved in the condensate. For example, in a chemical plant that manufactures fertilizers, the condensate may contain traces of ammonia or other valuable by – products. By recovering the condensate, the plant can recycle these chemicals, reducing waste and also potentially generating additional revenue.
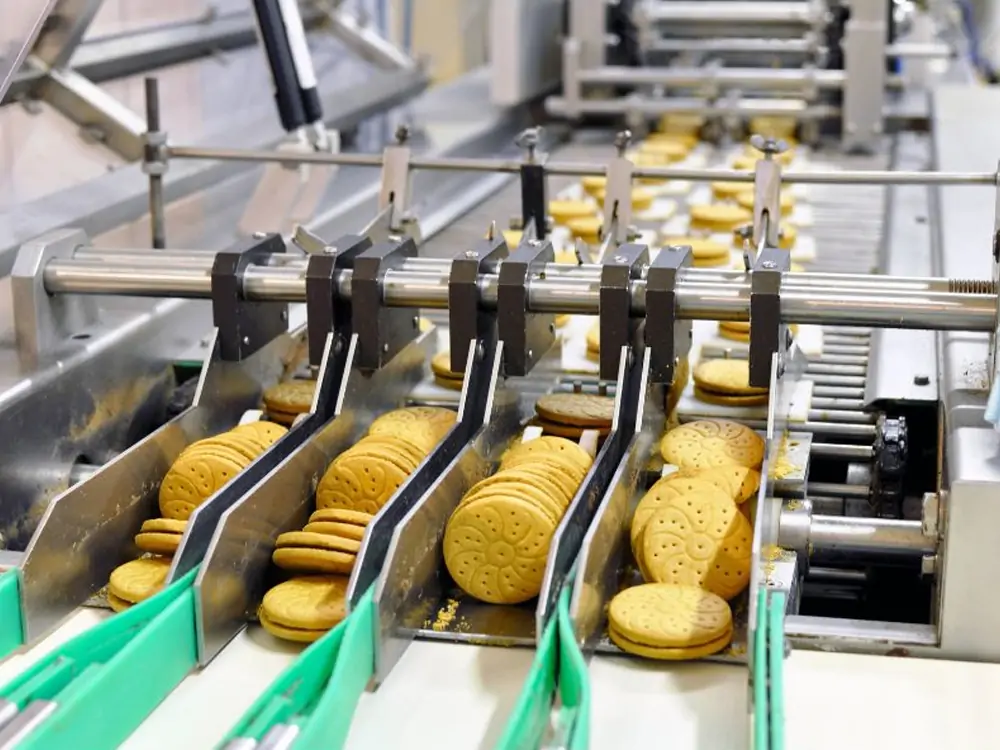
Food and Beverage Industry
In the food and beverage industry, steam is used for processes such as sterilization, cooking, and evaporation. The condensate recovery equipment can recover the condensate from these processes. In a brewery, for example, the condensate from the boiling wort can be recovered. This condensate is usually of high quality and can be used for other non – potable applications such as cleaning or pre – heating water for the next brewing cycle.
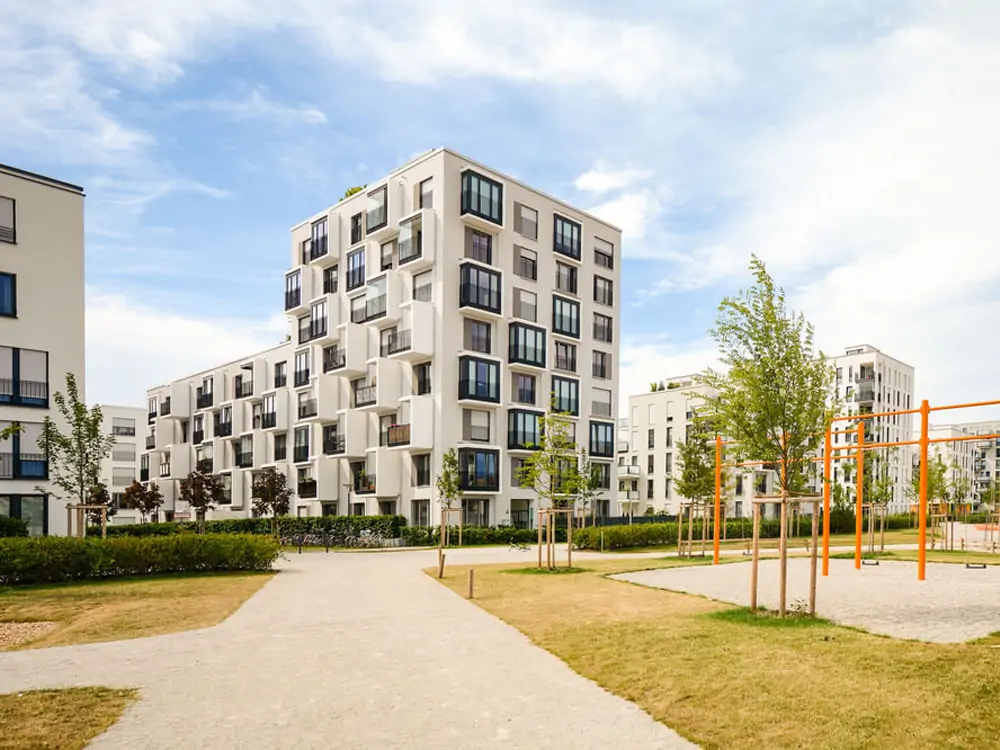
Textile Mills
extile mills use steam for processes like dyeing, drying, and fabric finishing. The condensate recovery equipment is used to recover the condensate from these steam – using operations. The recovered condensate can be used to pre – heat the water for subsequent textile processes. For example, in a fabric – drying operation, the condensate formed can be recovered and used to heat the water for the next dyeing batch. This not only saves energy but also reduces the amount of fresh water needed, which is beneficial for both cost – saving and environmental – friendly operations.
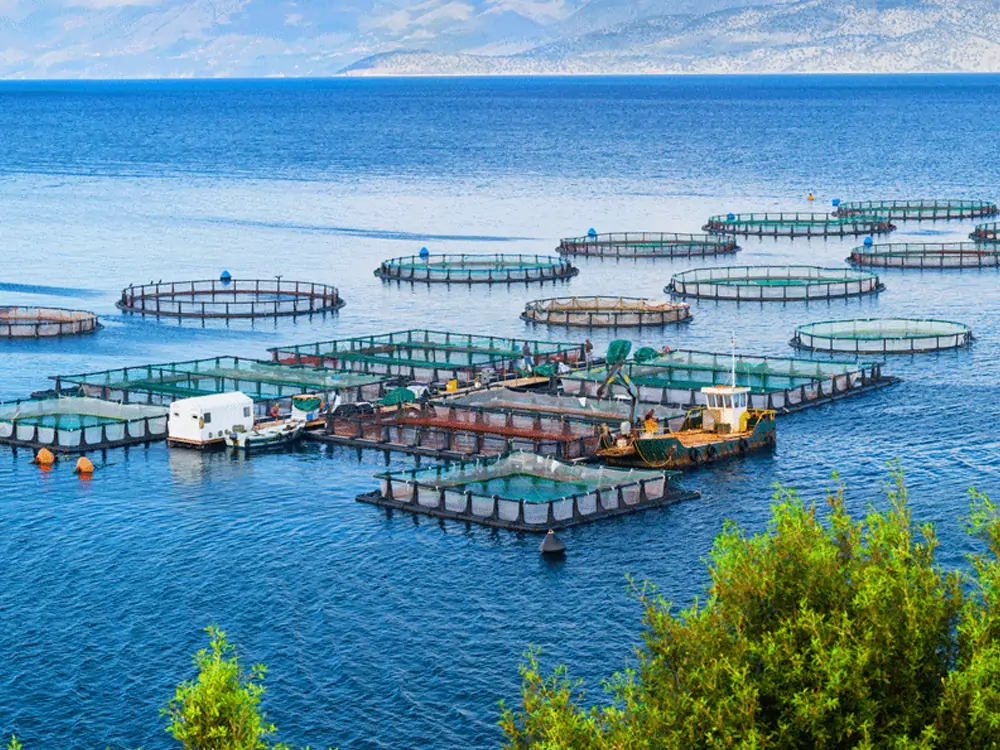
Power Generation Plants
In power generation plants, especially those that use steam turbines, a large amount of condensate is formed. The condensate recovery equipment is used to recover this condensate and recycle it back into the power generation cycle. The recovered condensate is usually fed back into the boiler feedwater system. By doing so, the plant can reduce the amount of makeup water required and also save a significant amount of energy.
condensate recovery equipment Details
Working Principle:
Condensate recovery equipment functions on several principles. Separation occurs as a cyclonic separator’s tangential entry induces a swirl and centrifugal force for condensate collection, and coalescing separation uses media to combine droplets. Energy recovery takes place in heat exchangers where hot condensate in tubes conducts heat to pre-heat surrounding fluid. Filtration uses physical barriers and ion-exchange resins adjust condensate quality, making it apt for reuse.
Separation Mechanism
Combines cyclonic and coalescing separation. Cyclonic uses tangential entry and centrifugal force; coalescing uses media to combine droplets for condensate purity.
Energy Recovery Component:
Utilizes shell-and-tube heat exchangers. Hot condensate in tubes transfers heat by conduction to surrounding fluid, saving energy in pre-heating.
Filtration and Treatment System:
Starts with mechanical filters for particulate removal. Then uses ion-exchange resins to adjust hardness and chemical dosing to neutralize corrosives for better condensate quality.
Condensate Collection and Storage:
Has a corrosion-resistant stainless steel tank. Level sensors monitor height and control inflow/outflow. Outlet allows pumping for further steps.
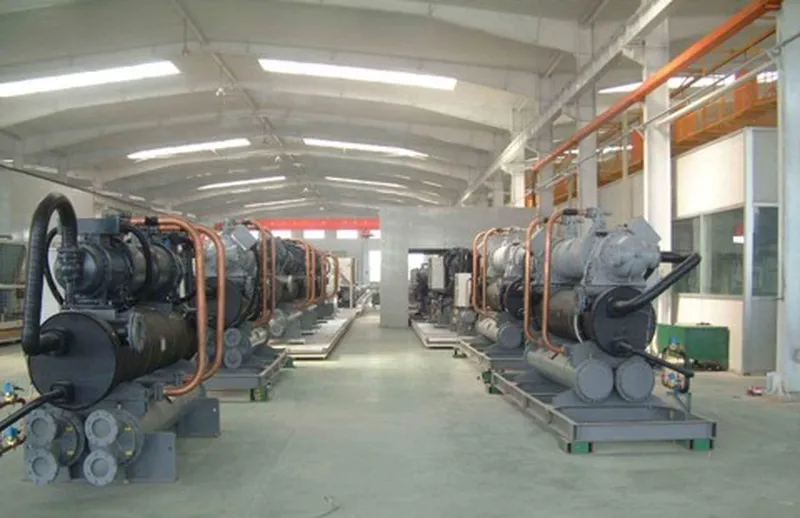
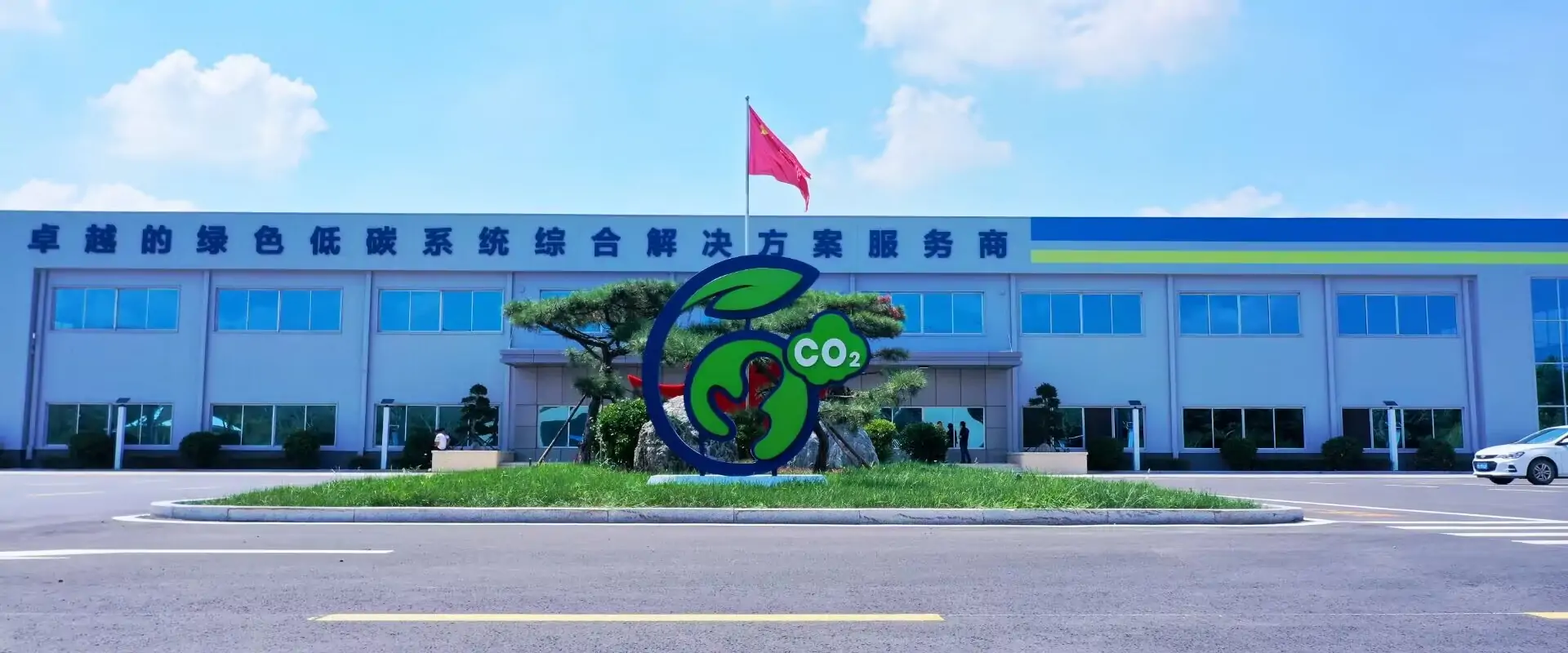
Efficiency and Performance:
condensate recovery equipment are multi-faceted. It exhibits high energy efficiency by recovering hot condensate to pre-heat feedwater, potentially reducing fuel consumption by 20% or more. A significant condensate recovery rate, often 90% or higher, is achieved through efficient separation and collection systems. The system pressure drop is kept low via proper piping and component design to ensure smooth fluid flow and prevent issues like reduced flow rates and increased energy consumption. Additionally, corrosion prevention, mainly through the use of corrosion-resistant materials like stainless steel, is vital for its long-term performance, safeguarding the equipment from the corrosive nature of condensate and ensuring its reliable operation over time.
Frequently asked questions
Most modern condensate recovery equipment is designed to handle both saturated and superheated steam. However, the equipment may need to be configured differently depending on the type of steam. For saturated steam, the focus is mainly on efficient condensate separation and energy recovery. For superheated steam, additional cooling mechanisms or pre – treatment steps might be required to bring the steam to a more suitable state for condensate recovery. Some advanced systems have built – in features to automatically adjust to different steam conditions, ensuring optimal performance regardless of the steam type.
Regular maintenance tasks include checking and cleaning the separation components such as cyclonic separators and coalescing filters to ensure proper condensate separation. The pumps should be inspected for wear and tear, and the impellers may need to be cleaned or replaced if clogged. The heat exchangers require periodic inspection for scale buildup and cleaning to maintain efficient heat transfer. Additionally, the level sensors in the condensate collection tank need to be calibrated regularly to ensure accurate measurement and control of condensate levels. Lubrication of moving parts and checking of electrical connections are also essential maintenance activities.
Condensate recovery equipment can have a positive impact on water quality. By recovering condensate and treating it, impurities such as dissolved solids, particulate matter, and some dissolved gases can be removed. The filtration and treatment processes within the equipment, like ion – exchange resins and chemical dosing, help adjust the hardness, pH, and other water quality parameters. This treated condensate, when reused, can reduce the need for fresh water intake and also prevent the introduction of new impurities into the system, which is beneficial for maintaining the overall water quality and reducing the risk of scale formation and corrosion in the associated equipment.
Yes, it is often possible to retrofit existing industrial plants with condensate recovery equipment. However, a detailed engineering assessment is required before the retrofit. The existing steam and condensate piping layout needs to be evaluated to ensure proper integration of the new equipment. Space availability for installing the recovery equipment, compatibility with the existing steam generation and usage systems, and any potential impacts on the plant’s production process during the retrofit need to be considered. In some cases, minor modifications to the existing infrastructure may be sufficient, while in others, more extensive changes might be necessary, but the potential energy savings and environmental benefits usually make the retrofit a viable option.