Core Advantages
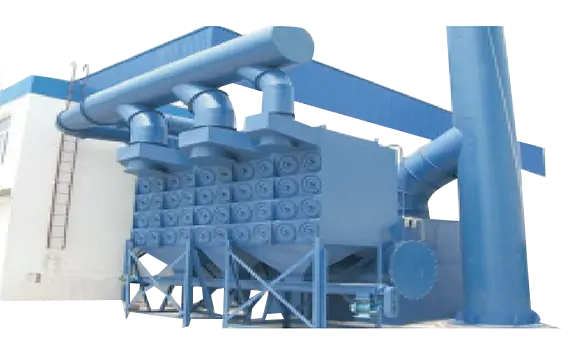
Efficient Filtration and Capture
- The system uses advanced filtration technologies, such as HEPA filters, electrostatic precipitators, or bag filters, to effectively capture and remove harmful dust particles and fumes from the air, ensuring cleaner and safer working environments.
Energy Efficiency and Cost Savings
- With optimized airflow systems and regenerative filters, the equipment reduces energy consumption during operation, leading to lower operating costs while maintaining high performance in industrial and commercial settings.
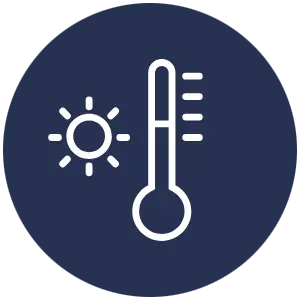
Improved Air Quality
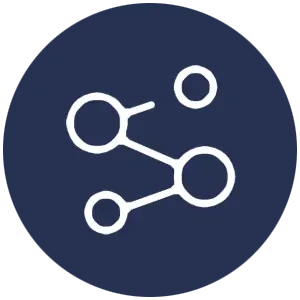
Regulatory Compliance
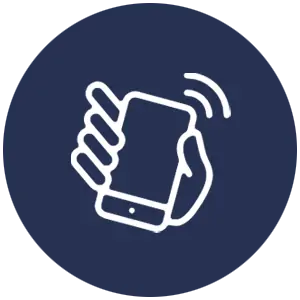
Protection of Equipment and Machinery
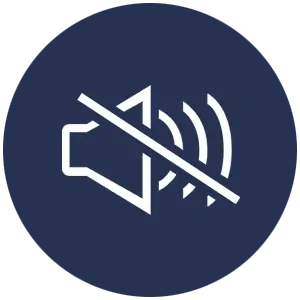
Energy Efficiency
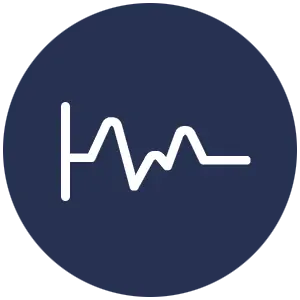
Versatility
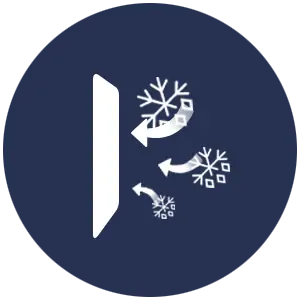
Enhanced Workplace Safety
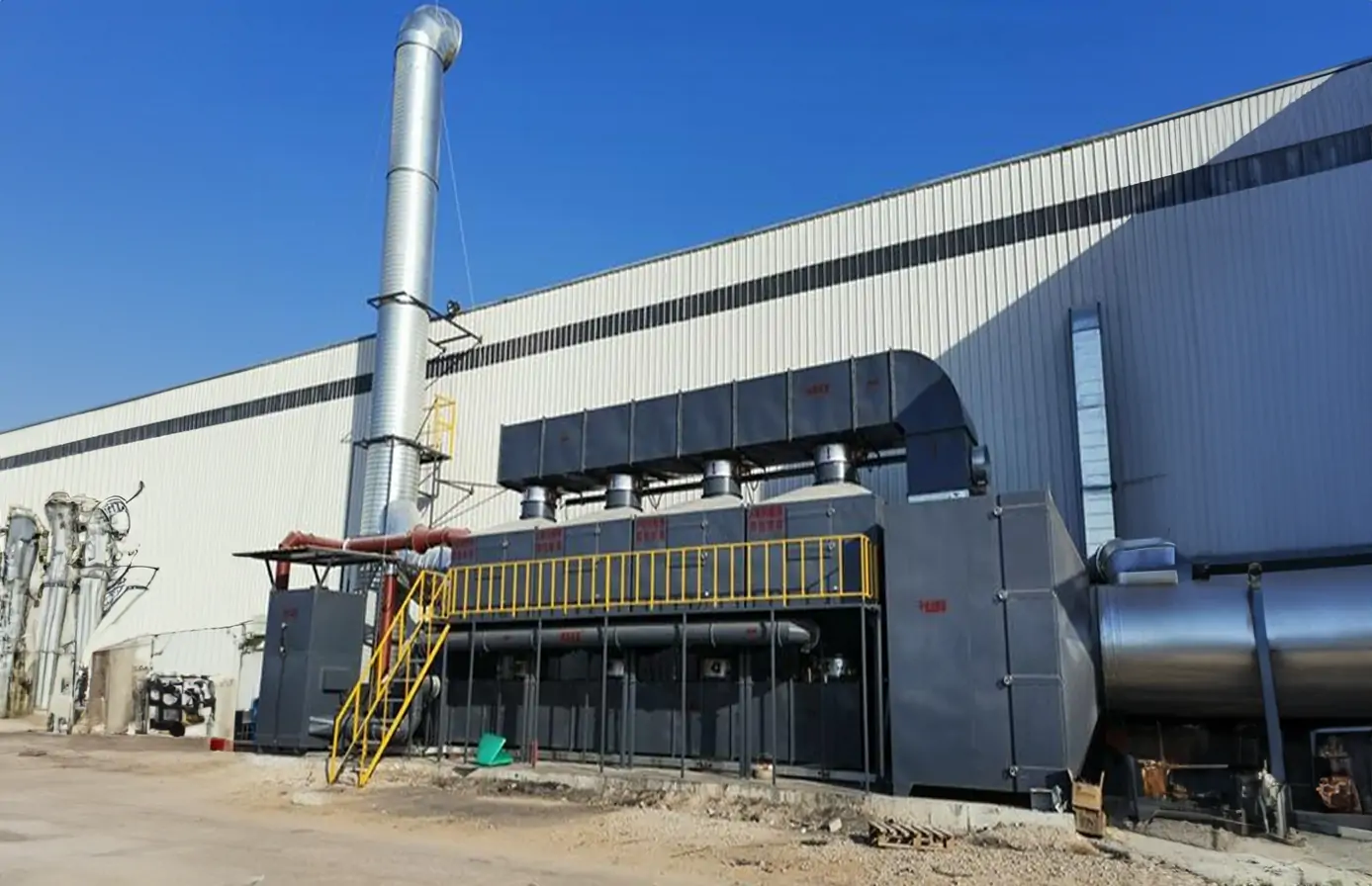
Improved Air Quality
- The equipment effectively captures and removes harmful fumes and dust particles from the air, significantly enhancing indoor air quality and creating a safer working environment for employees.
Regulatory Compliance
- Many industries are subject to strict regulations regarding air quality and emissions. Fume and dust treatment systems help businesses meet these regulatory requirements by ensuring that pollutants are adequately filtered before being released into the atmosphere. Compliance with environmental standards reduces the risk of penalties and legal liabilities, fostering a positive corporate image and enhancing a company’s reputation.
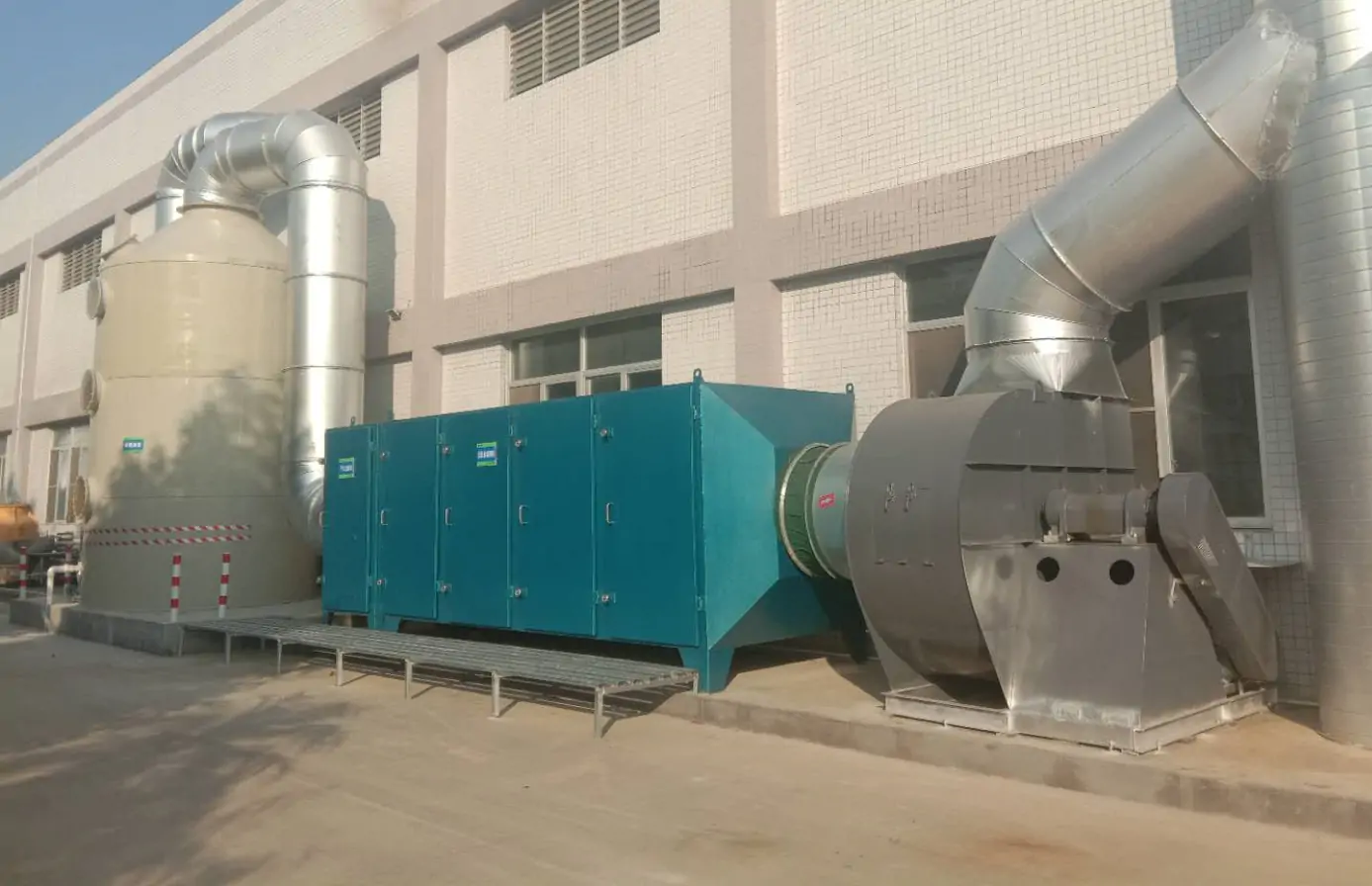
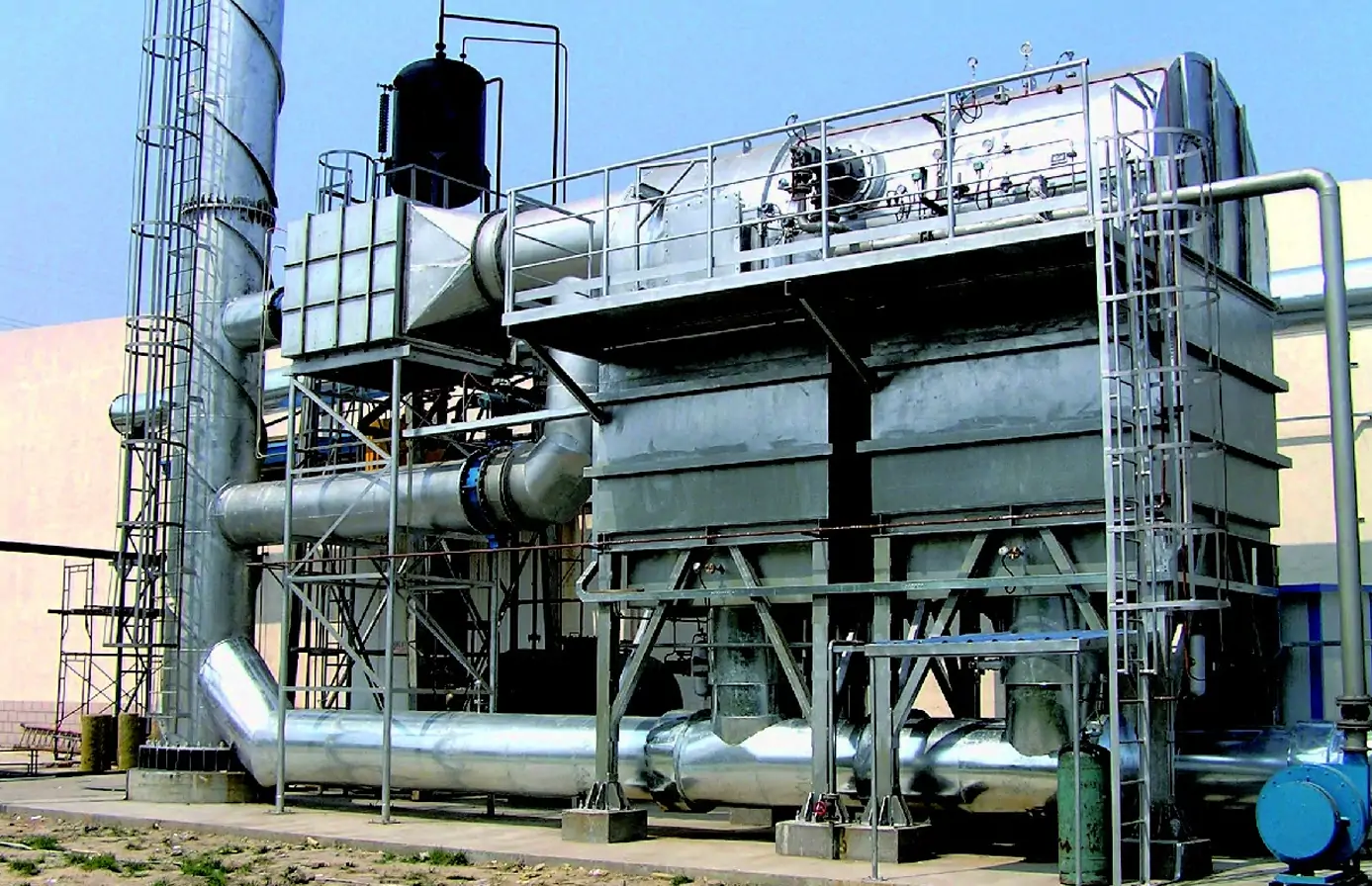
Protection of Equipment and Machinery
- Dust and particulate buildup can lead to equipment malfunctions and increased maintenance costs. Fume and dust treatment systems minimize this buildup by capturing contaminants at the source, thus extending the lifespan of machinery and equipment. By maintaining a cleaner environment, these systems reduce the frequency and cost of repairs, ensuring smoother operations and lower downtime.
Energy Efficiency
- Modern fume and dust treatment equipment is designed with energy efficiency in mind. Features such as variable speed fans, energy recovery systems, and optimized airflow pathways help minimize energy consumption during operation. This not only reduces operational costs but also contributes to sustainability efforts by lowering the overall carbon footprint of the facility.
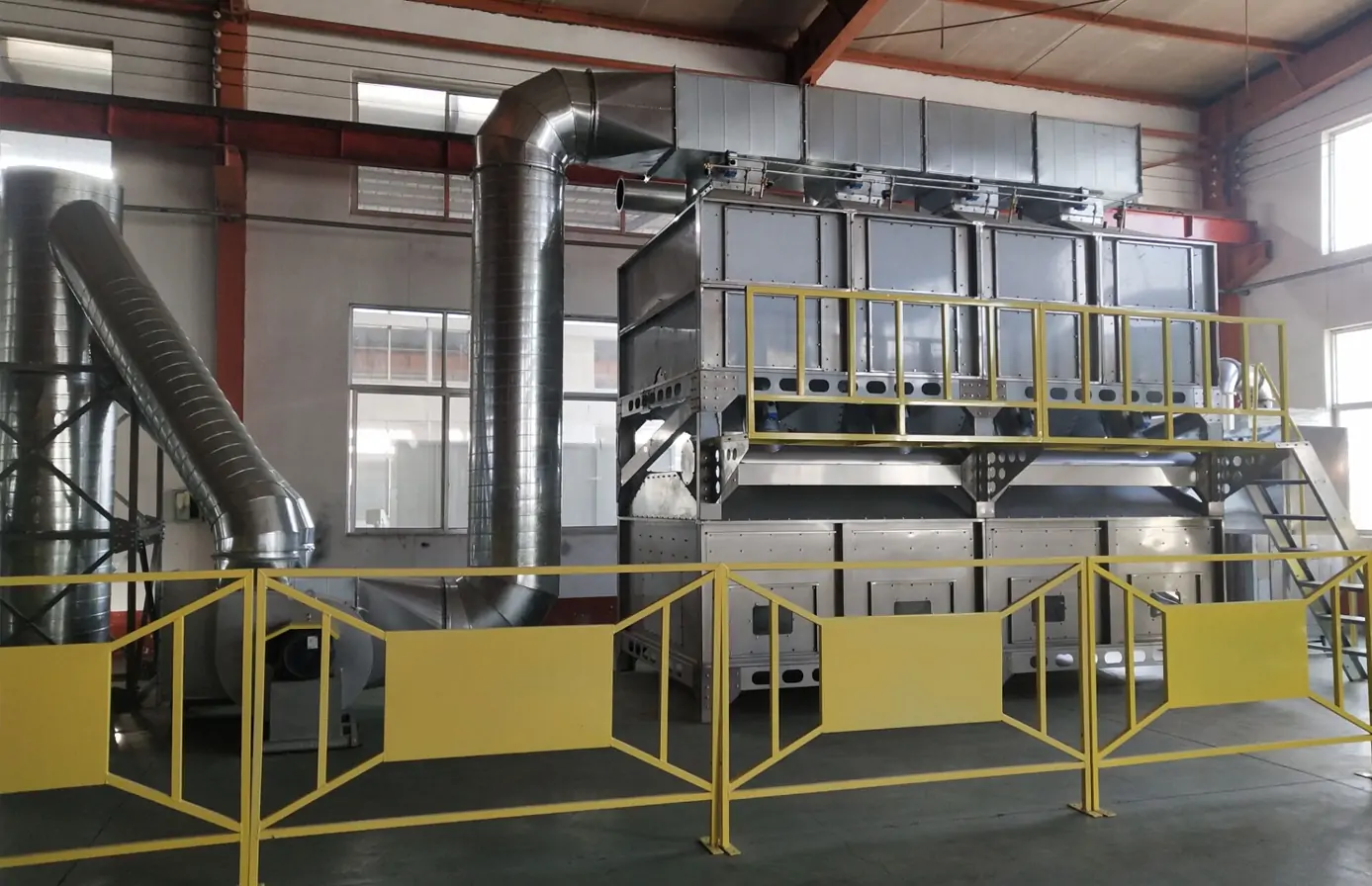
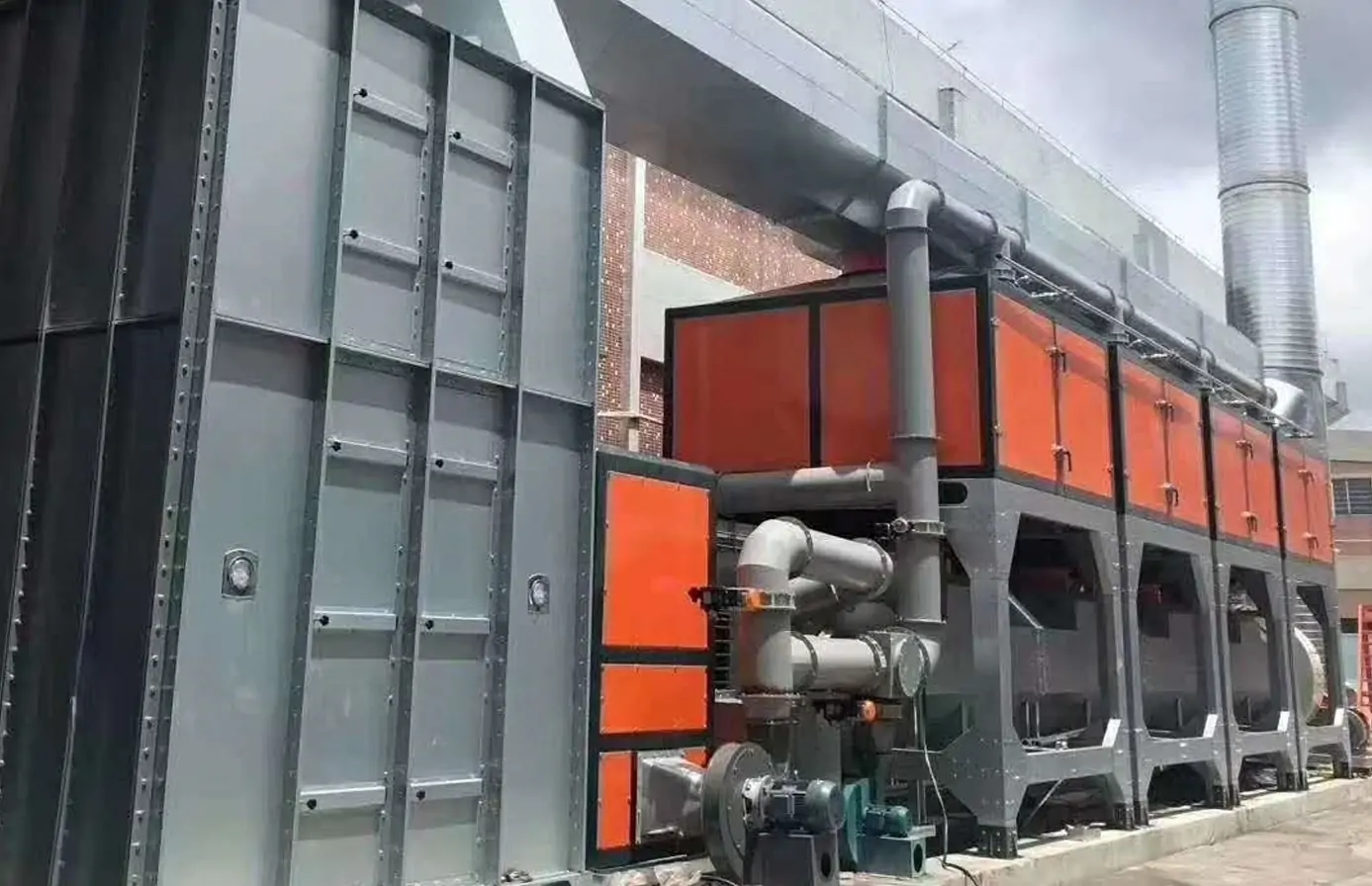
Versatility
- Fume and dust treatment equipment can be customized for various applications across multiple industries. Whether used in manufacturing, construction, automotive, pharmaceuticals, or food processing, these systems can be adapted to handle specific types of contaminants and varying airflow requirements. Their versatility allows businesses to implement effective air quality solutions tailored to their unique operational needs.
Enhanced Workplace Safety
- By effectively reducing harmful fumes and dust in the workplace, fume and dust treatment equipment contributes to a safer working environment. This leads to fewer workplace accidents and health-related absenteeism, ultimately promoting employee well-being and productivity. A safer workplace fosters employee morale and can improve retention rates, as workers feel valued and protected in their environment.
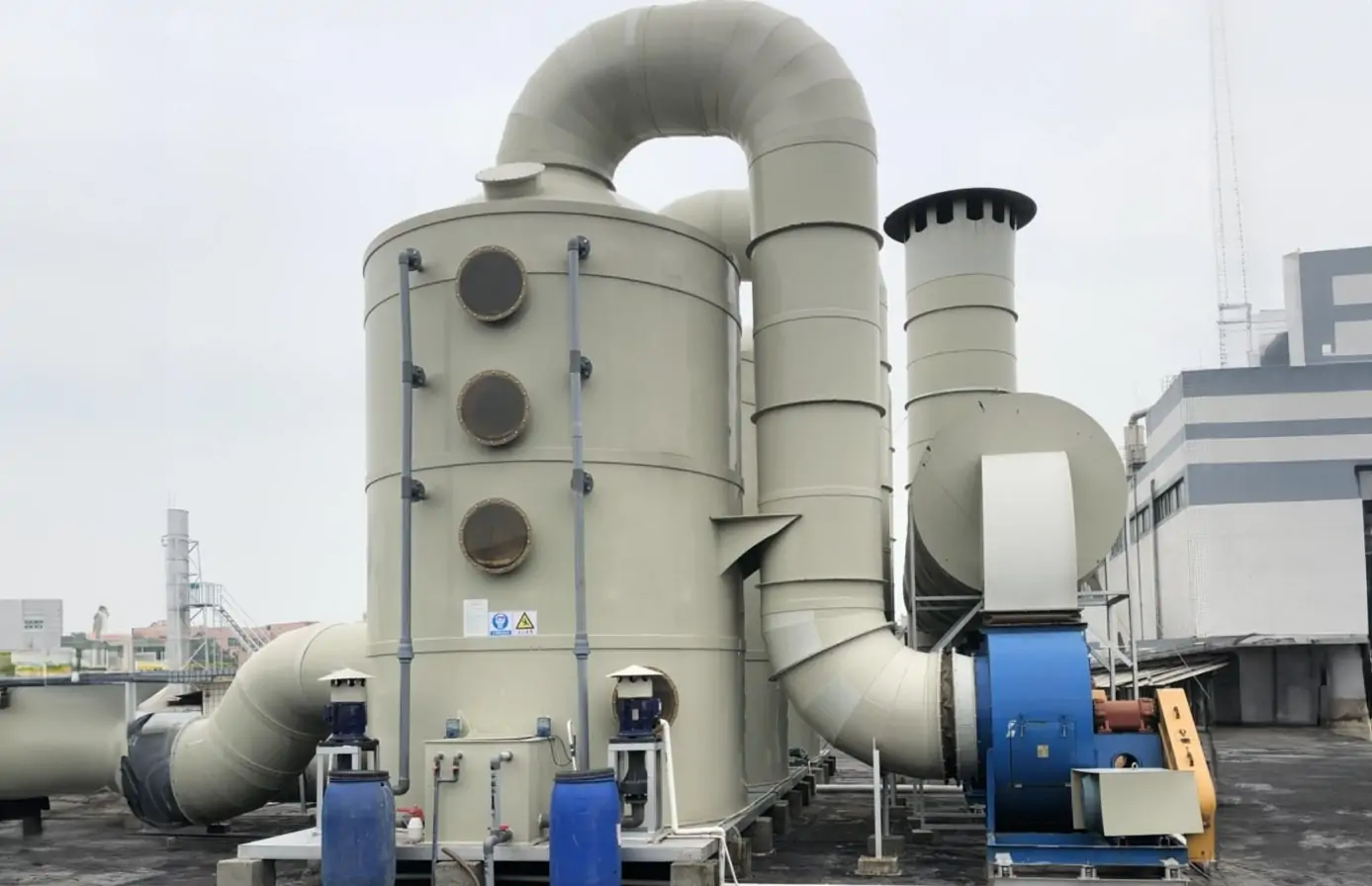
Product Specifications
Product Specification | Details | Product Specification | Details |
Heating Power | 6.0 kW | Energy Efficiency Rating | A++ |
Refrigerant Type | R410A | Applicable Area | 50-150㎡ |
Power Supply Voltage | 220V / 50Hz | Noise Level | ≤25 dB |
Dual Inverter Technology | Supported | Smart Temperature Control | Supported |
Remote Control | Mobile App Remote Control | Auto Defrost Function | Supported |
Operating Temp Range | -15℃ to 45℃ | Weight | 40 kg |
Dimensions (L x W x H) | 850mm x 300mm x 650mm | Installation Method | Ceiling / Wall Mounted |
fume and dust treatment equipment Feature and Application:
Application:
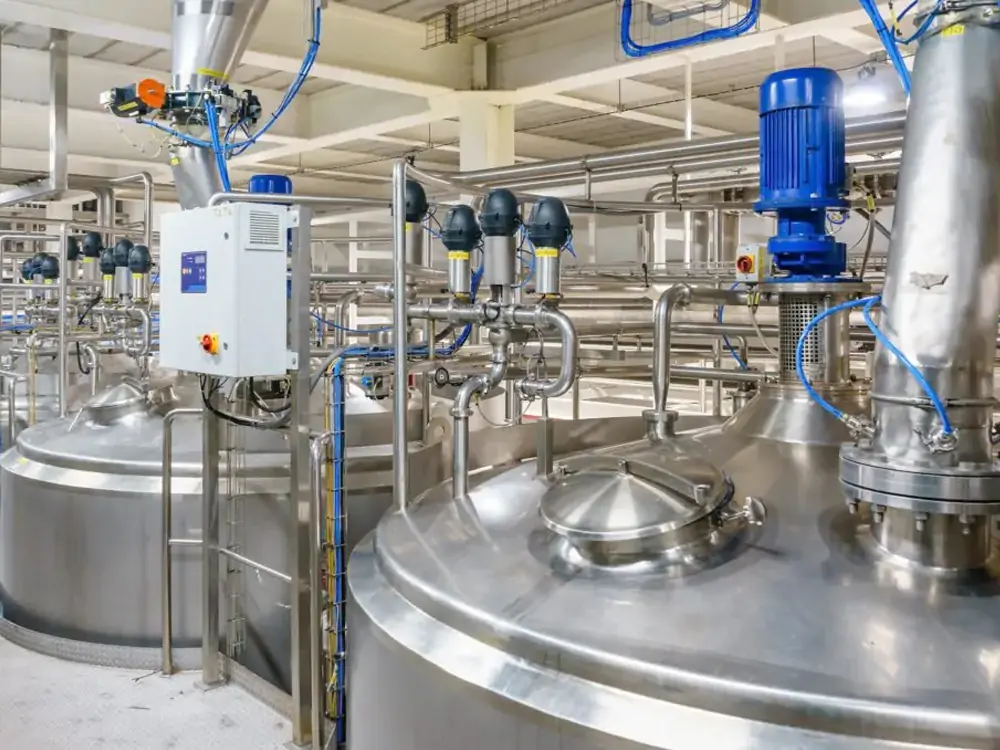
Manufacturing Plants
Used to capture and filter airborne contaminants generated during production processes, such as metalworking, woodworking, and chemical manufacturing. This helps maintain a safe working environment and protects machinery from dust buildup
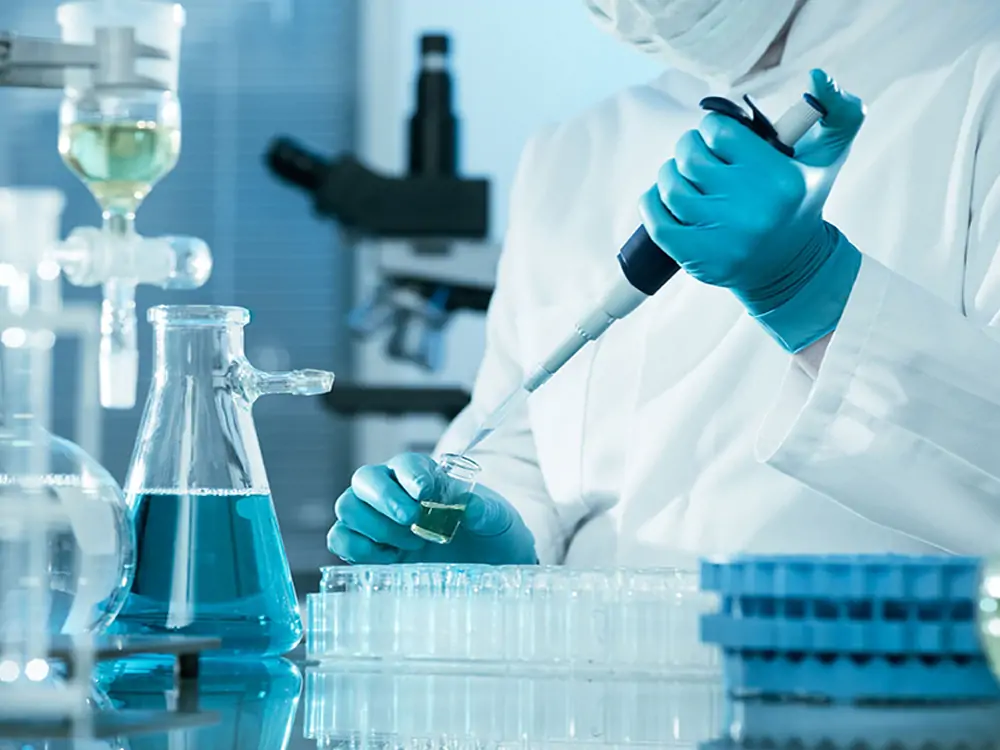
Pharmaceutical Facilities
Essential for maintaining clean air conditions in drug manufacturing and laboratory environments. These systems prevent contamination and ensure compliance with stringent regulatory standards for air quality.
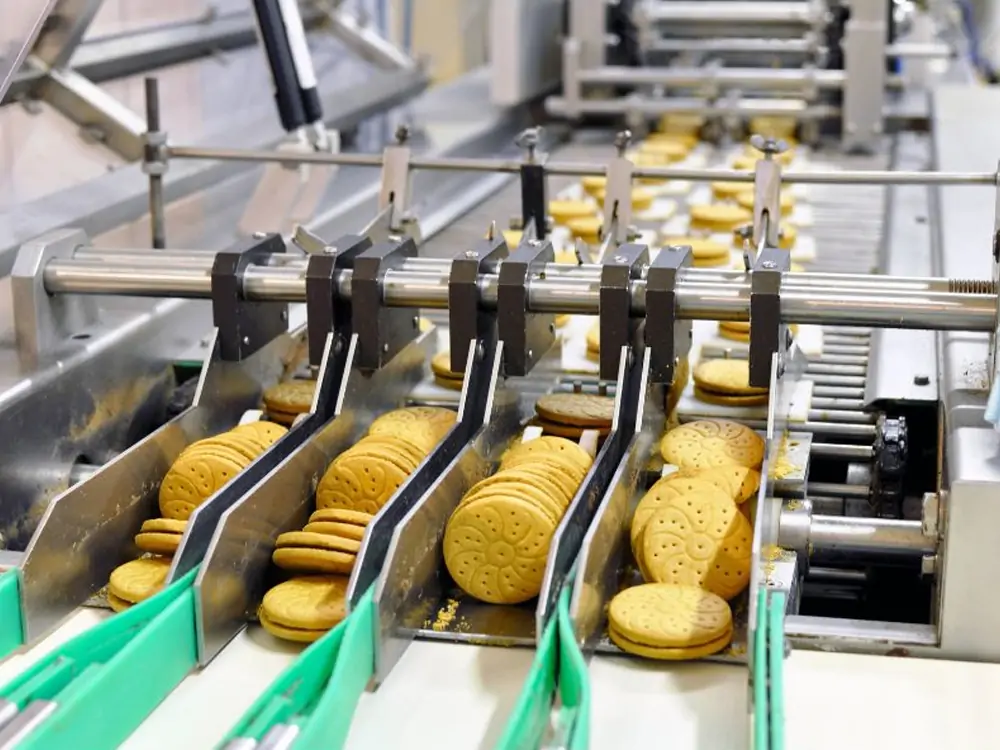
Food Processing:
Employed to control dust and fumes generated during food production and packaging. Effective air treatment helps prevent contamination and maintains hygiene standards in food processing environments.
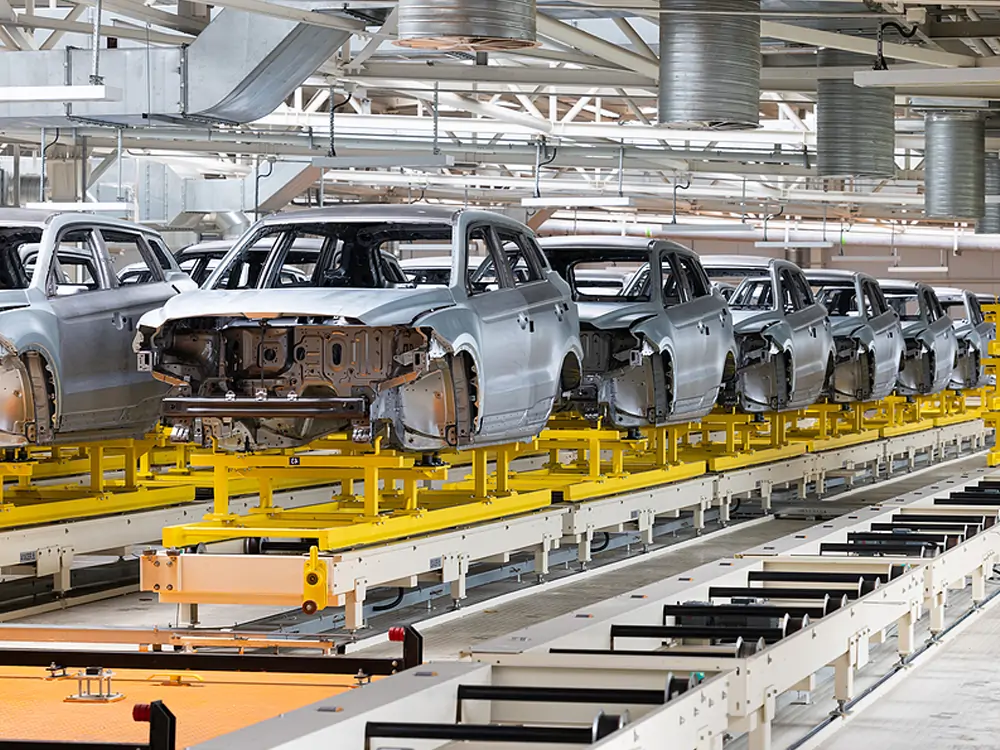
Automotive Industry:
Used in paint shops and assembly lines to filter out harmful fumes and particulate matter generated during manufacturing and finishing processes. This helps ensure worker safety and enhances product quality.
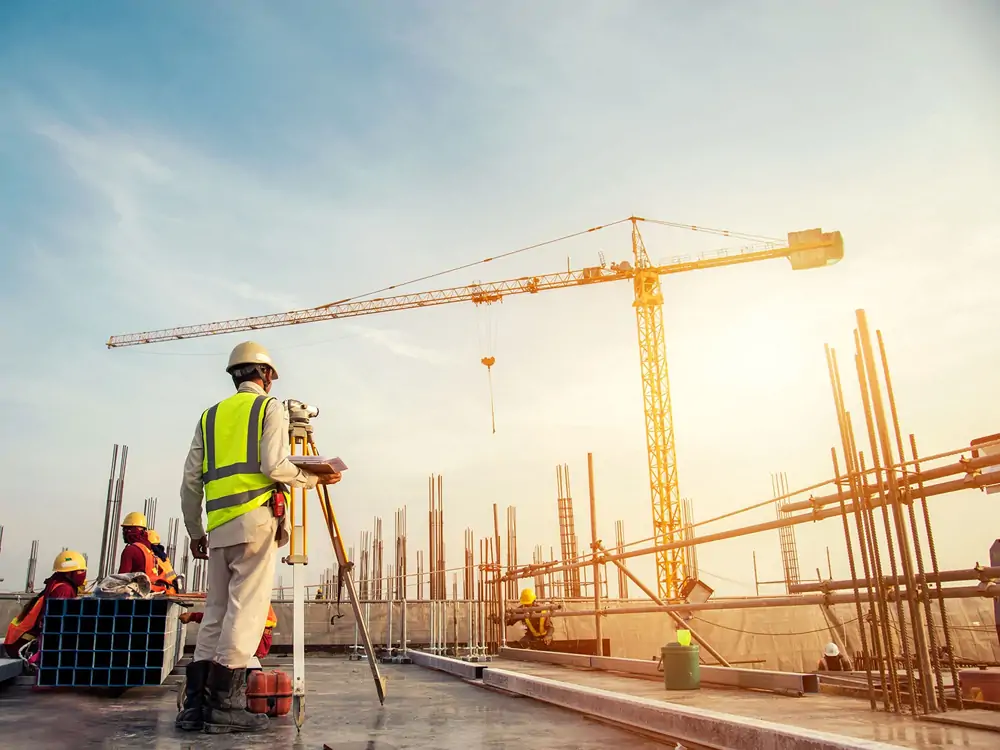
Construction Sites:
Utilized for controlling dust and harmful particles released during construction activities. Fume and dust treatment equipment helps minimize air pollution and protects workers and nearby residents from exposure to hazardous materials.
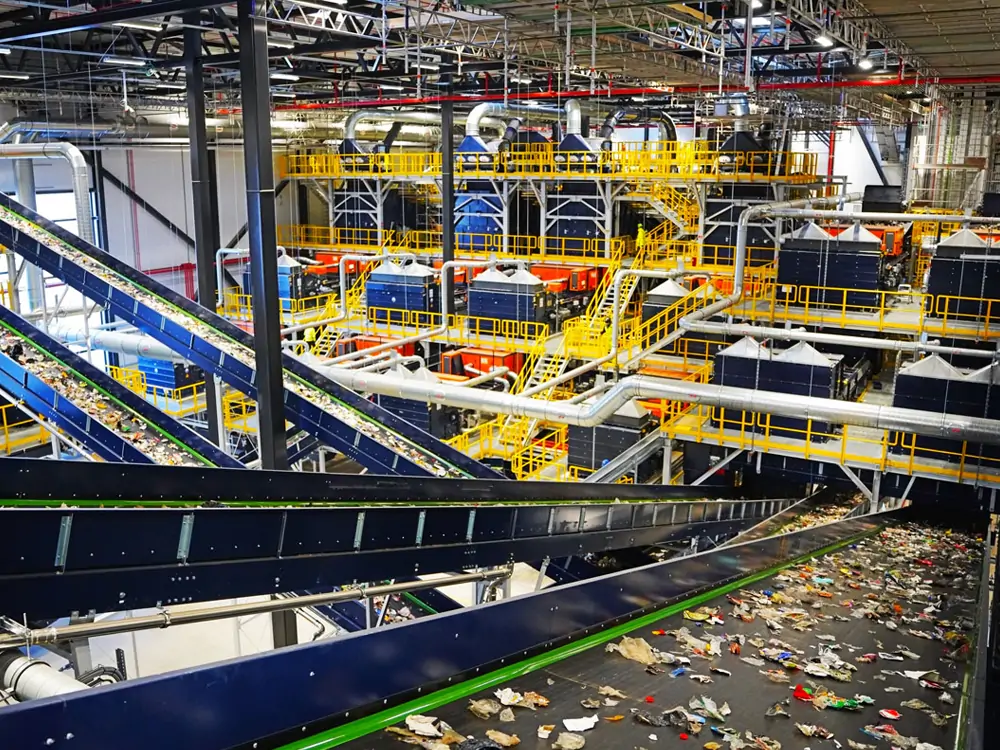
Waste Management and Recycling Facilities
Employed to manage odors, fumes, and dust produced during the sorting and processing of waste materials. These systems help maintain a cleaner environment and reduce health risks associated with exposure to airborne contaminants in waste management operations.
fume and dust treatment equipment Details
Working Principle:
fume and dust treatment equipment involves several key processes designed to capture and remove airborne contaminants effectively. The basic steps include:
Air Intake:
Contaminated air from the workspace is drawn into the system using exhaust fans or blowers. This initiates the air treatment process.
Filtration:
As the air passes through various filtration modules, including HEPA filters, activated carbon filters, or electrostatic precipitators, particles, dust, and harmful fumes are trapped. These filters are designed to capture a wide range of contaminants, ensuring high efficiency in removing particulate matter and volatile organic compounds (VOCs)
Dust Collection:
The collected dust and particulates are gathered in a dust collection chamber or bag. This prevents the contaminants from being released back into the environment, maintaining cleaner air quality.
Expansion and Recycling:
The refrigerant expands and cools through the expansion valve, returning to its original state and repeating the process.
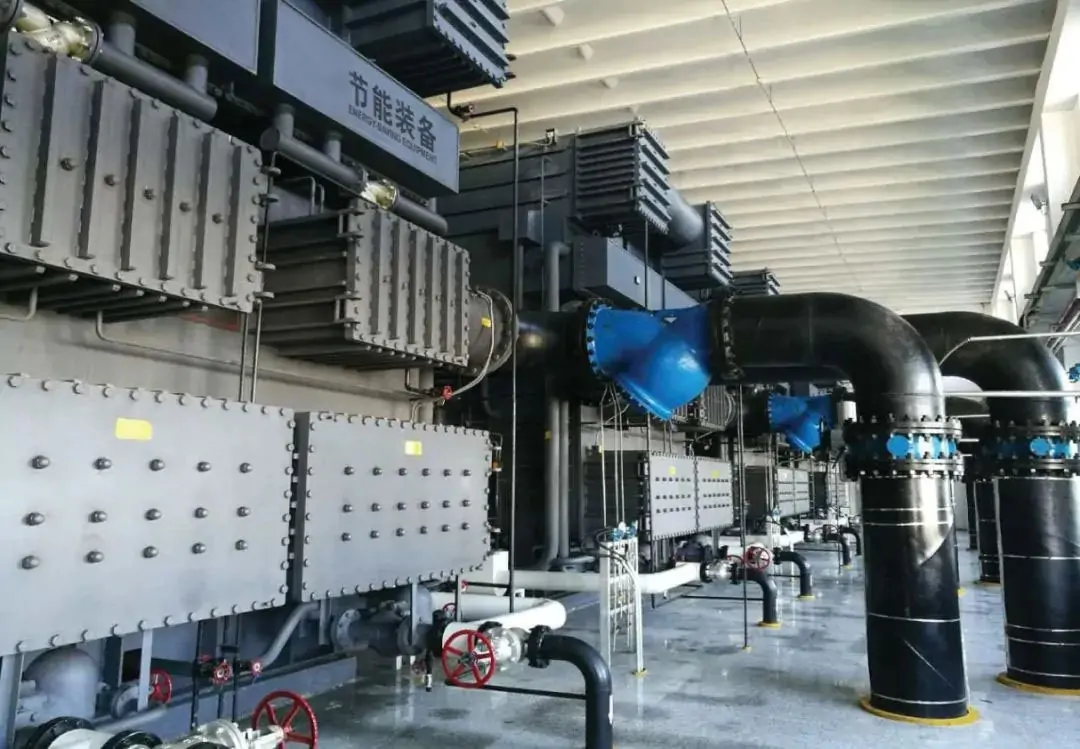
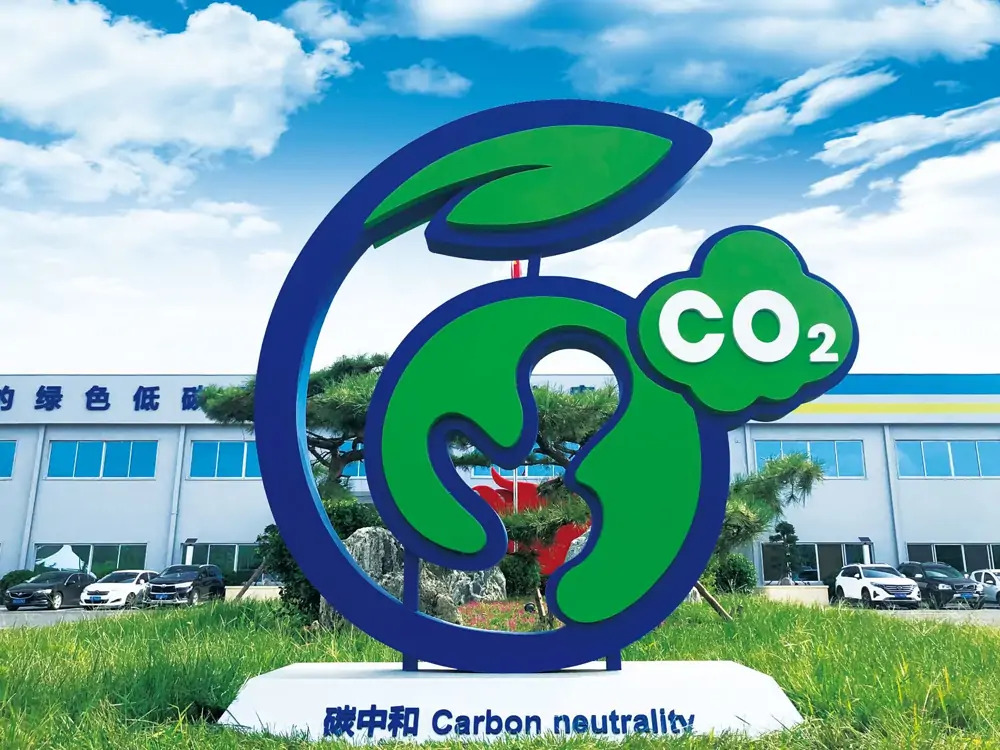
Efficiency and Performance:
fume and dust treatment equipment are centered on its ability to effectively capture and filter airborne contaminants while minimizing energy consumption. Advanced filtration technologies, such as HEPA and activated carbon filters, provide high removal efficiency, trapping fine particles, dust, and harmful fumes. These systems ensure compliance with air quality standards while safeguarding worker health.
Energy-efficient fans and airflow designs optimize performance, reducing energy consumption during operation. Additionally, some systems incorporate energy recovery technologies, like heat exchangers, which reclaim energy from exhaust air, lowering operational costs. The combination of efficient contaminant removal and energy-saving features ensures a balanced performance, making the equipment both effective and cost-efficient for various industrial applications.
Frequently asked questions
The system uses fans to draw in contaminated air, passes it through filters (HEPA, activated carbon, etc.) to remove dust and fumes, and either recirculates the clean air or exhausts it outside.
Industries such as manufacturing, pharmaceuticals, food processing, automotive, construction, and waste management benefit from fume and dust treatment systems for improved air quality and regulatory compliance.
Many systems feature energy-saving components like variable-speed fans and heat recovery technologies, which help reduce energy consumption and operational costs.
Regular maintenance involves cleaning or replacing filters, checking airflow and system performance, and ensuring dust collection units are emptied or cleaned as needed.
Yes, fume and dust treatment equipment is designed to handle both particulate matter (dust) and gaseous contaminants (fumes) effectively through various filtration methods.
Filter life depends on usage and the amount of contaminants, but regular inspections are recommended. HEPA filters, for example, may need replacement every 6-12 months, while activated carbon filters can last longer depending on exposure.